Advanced Surface Functionalization for Machinery Enhanced Lifetime – Fun4MEL
The objective is to investigate how to enhance the lifetime of machine parts through surface functionalization.
2023 – 2026
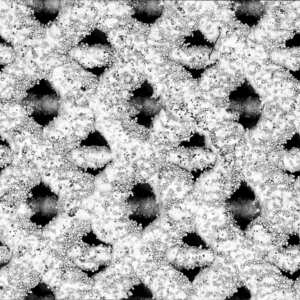
The objective is to investigate how to enhance the lifetime of machine parts through surface functionalization.
2023 – 2026
Circular handheld machines; from an environmental and human perspective (Zero Vibration Circularity)
2024 – 2027
The project's goal is the circular use of plastic in cars through reuse and recycling.
2023 – 2025
Better work instructions for more efficient and inclusive work
2022 – 2025
Dynamic SALSA - Dynamic Scheduling of Assembly and Logistics Systems using AI
2023 – 2026
The project's goal is to assist industry enabling sustainable work for operators during assembly of wire harnesses.
2022 – 2025
Realizing the future of maintenance in battery production for a sustainable and competitive battery industry.
2023 – 2026
Objective: develop a condition monitoring system to support the operation of hydraulic pumps in servo presses
2023 – 2025
WELDVISI will create a new sensor-based assistance system for manual manufacturing with real-time cognitive feedback and documentation of parameters.
2022 – 2025
We use cookies to improve the user experience and analyze user behavior. You can read more on the page About cookies.