Peter Almström
Docent
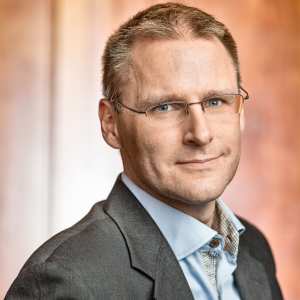
Project time: 2015 – 2016
Budget: 750 000 kr
Funding: SIP Produktion2030
The purpose of this project was to explore how accurate operation times can be ensured and kept updated by integrating the systems for process planning, data acquisition and business planning. The objective w as to develop a DM concept that includes a complete prototype and decision model for Time Data Management for Smart Factories. This goal has been achieved and a functioning prototype system is currently operational.
As stated, a prototype system is operational at the final assembly of Volvo Penta´s plant in Vara. Further w ork is underw ay to implement the system in more departments. The analysis of the system and the development of decision-making model has resulted in a publication in a scientific journal which is currently under review (round 2). The project results w ill be disseminated in popular formats via example. NyTeknik, trade magazine or the like when the publication is accepted
An extended current state analysis included operational training of the existing system, analysis and modeling of historical monitoring data and an extended literature for mapping the area. This constituted the basis for the requirement specifications for the prototype system and the development of decision-making model. MVV Information Technology further developed and integrated existing systems to the prototype that is operational today. During the process several interview s w ith key people such as production engineers and system developers w as also conducted.
2017 – 2018
2015 – 2015
2015 – 2016
Tooling constitutes a significant part in the economical investment of the hot stamping process. Significant benefits in production economy and environmental benefits can be attained by improving the tribological performance in hot forming operations of automotive components. The main idea of this project is to create tailored tool surfaces on dies made from cheaper and easier to manufacture tool steel for the hot stamping of ultra-high strength steels.
2015 – 2018
2017 – 2018
2014 – 2017
2014 – 2017
2017 – 2018
2016 – 2016
2015 – 2016
Development of a thermo-chemical test bed and implemenation of results for chosen processes and applications
2019 – 2022
2014 – 2017
2017 – 2018
2014 – 2017
2017 – 2019
2017 – 2018
2015 – 2016
2014 – 2014
2017 – 2021
2016 – 2017
RemProLife aims at improving the use of life-cycle information to achieve more efficient remanufacturing from economic and ecological perpectives.
2013 – 2016
2015 – 2016
2016 – 2019
2015 – 2016
2015 – 2015
2016 – 2016
2013 – 2016
The project focuses on economic and environmental sustainability and increased industrial competitiveness.
2017 – 2018
2014 – 2017
2013 – 2017
2017 – 2020
2015 – 2016
2016 – 2017
2013 – 2016
2015 – 2016
With globalization and other megatrends as demographic changes and climate change, more knowledge is needed regarding production in an international perspective. PADOK Study Visit in India 2016 have given an increased knowledge regarding how production is conducted in India, some of the challenges producing companies in that region is facing and how Swedish companies interested in investing in production in India could act to establish themselves in the region.
2016 – 2016
2017 – 2018
2016 – 2018
2014 – 2018
The SAPPA project is about innovative cloud-based predictive and preventive maintenance systems, improving availability of products and production systems.
2014 – 2016
2017 – 2018
2017 – 2018
2016 – 2016
2014 – 2016
2017 – 2020
2015 – 2017
2016 – 2018
2017 – 2018
2015 – 2016
Increased sustainability and cost effectiveness through improved strategic decision-making in production issues based on new metrics system for production and development.
2015 – 2017
2013 – 2017
2016 – 2016
Every manufacturing company measure and control production performance with a system of KPIs. The aim of the SMART-PM project is to investigate and demonstrate new ways of collecting data, transforming data to information and introducing new decision tools based on valid information and economic models of the production systems.
2018 – 2020
2015 – 2018
2015 – 2016
SeeCut focuses on cost-efficient production systems for secure collection, analysis, visualization, storage and sharing of production data. The project addresses the integration of new signals and sensors. For advanced products, like jet engine components, collecting data during manufacturing and usage is essential for quality assurance and remanufacturing. The project goals are to identify key technical requirements related to production data for use in digitalized value chains, define means to ease the run-time integration of new signals and data streams from manufacturing machinery and sensors, and define how to securely and cost-efficiently share data through the value chains in circular production.
2019 – 2019
Reduced lead times and improved performance for tooling through innovative manufacturing and assembly strategies as well as optimised design enabled by use of additive manufacturing (AM).
2016 – 2018
2014 – 2017
2015 – 2016