Gunilla Sivard
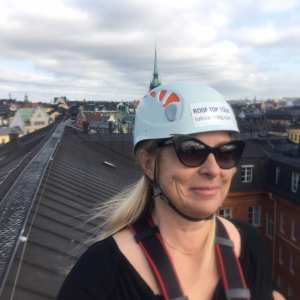
Project time: 2013 – 2017
Budget: 11 520 000 SEK
Funding: SIP Produktion2030
The goal of the project w as to support innovation by providing an environment for collaboration and learning through modeling, simulation and visualization of a production system.
A framew ork for innovation based on a digital factory w as developed. The framew ork consists of an infrastructure for building digital factories, a demonstrator of an implemented digital factory, plus underlying principles for representing and presenting production information. A technical infrastructure exists which can be detailed according to company needs:
http://ifactory.iip.kth.se/eif/
Contribution to an IT-system independent methodology:
1) Based on theories of computer science and visual studies the foundation for a new theory concerning representation and presentation of production information from a user perspective.
2) Generic digital factory system architecture – for implementing digital factories.
3) Digital factory of a production system that is concrete and sufficiently complex, where various issues can be exemplified and connected from various know ledge background. This can be used in w orkshops concerning the development of production systems.
Relevant issues w ere identified in cooperation w ith the industrial companies, and a digital factory for a concept vehicle w as implemented to reflect the issues and principles.
For coordination, w e have used theories of Boundary object which in our case consists of: Graphical models embodying the concepts that are common to a production system, Information models that describe the concepts embodied in the system’s data model, Demonstrator of a factory that is concrete and moderately complex, where various issues can be exemplified and interconnected.
2015 – 2017
2017 – 2019
2016 – 2016
Increased sustainability and cost effectiveness through improved strategic decision-making in production issues based on new metrics system for production and development.
2015 – 2017
2016 – 2018
2015 – 2018
2015 – 2015
2015 – 2016
2015 – 2016
The SAPPA project is about innovative cloud-based predictive and preventive maintenance systems, improving availability of products and production systems.
2014 – 2016
2016 – 2016
2017 – 2021
2015 – 2015
2015 – 2016
Tooling constitutes a significant part in the economical investment of the hot stamping process. Significant benefits in production economy and environmental benefits can be attained by improving the tribological performance in hot forming operations of automotive components. The main idea of this project is to create tailored tool surfaces on dies made from cheaper and easier to manufacture tool steel for the hot stamping of ultra-high strength steels.
2015 – 2018
2015 – 2016
2014 – 2017
2015 – 2016
2017 – 2018
2013 – 2016
2017 – 2020
2016 – 2018
2016 – 2016
The main idea of the project is to investigate and demonstrate how the digitalized and proven systems and technologies of the Process Industry, like CPAS, can be used in DM to improve competitiveness and drive growth
2017 – 2019
2014 – 2017
2014 – 2017
Every manufacturing company measure and control production performance with a system of KPIs. The aim of the SMART-PM project is to investigate and demonstrate new ways of collecting data, transforming data to information and introducing new decision tools based on valid information and economic models of the production systems.
2018 – 2020
2015 – 2016
2014 – 2014
2016 – 2016
2017 – 2018
2017 – 2020
2017 – 2018
2017 – 2018
2016 – 2019
2015 – 2016
2016 – 2017
Reduced lead times and improved performance for tooling through innovative manufacturing and assembly strategies as well as optimised design enabled by use of additive manufacturing (AM).
2016 – 2018
2014 – 2016
2015 – 2016
2015 – 2016
2017 – 2018
2013 – 2017
2017 – 2018
The project focuses on economic and environmental sustainability and increased industrial competitiveness.
2017 – 2018
2015 – 2016
2017 – 2018
2014 – 2017
2014 – 2017
With globalization and other megatrends as demographic changes and climate change, more knowledge is needed regarding production in an international perspective. PADOK Study Visit in India 2016 have given an increased knowledge regarding how production is conducted in India, some of the challenges producing companies in that region is facing and how Swedish companies interested in investing in production in India could act to establish themselves in the region.
2016 – 2016
2013 – 2016
2017 – 2018
2015 – 2016
2017 – 2018
Methods for 3D scanned digital twins for efficient development and installation of production facilities at SMEs
2018 – 2021
2014 – 2018
2014 – 2017
2016 – 2017
RemProLife aims at improving the use of life-cycle information to achieve more efficient remanufacturing from economic and ecological perpectives.
2013 – 2016