Casper Wickman
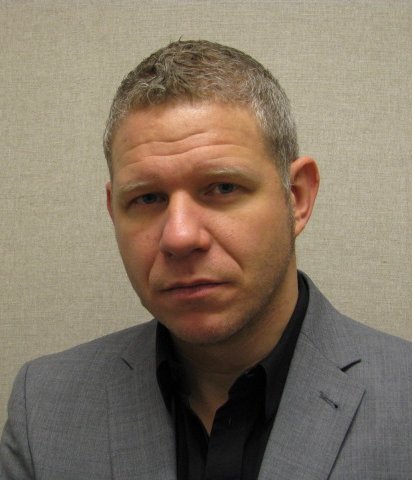
Project time: 2015 – 2016
Budget: 333 800 kr
Funding: SIP Produktion2030
The purpose w ith this project is to predict the occurrence of squeak and rattle virtually w ith different types of analysis from CAD based analysis to advanced CAE-based analysis. The mobility project has aimed to exchange know ledge betw een Chalmers, Volvo Cars and Ziegler Instruments in the prediction of squeak and rattle. Volvo Cars and Chalmers has trained Ziegler in CAE-based analysis and Ziegler has trained Chalmers and Volvo in the CAD-based analysis. A total of eight people participated in the exchange. Now each part can apply respective methods individually
For Volvo Cars, the effect of exchange is that resource-intensive CAE activities can be replaced w ith simple CAD-based methods to identifiable potential problems. This results in more efficient use of resources and shorter time loops analysis.
For Ziegler, the exchange has resulted in that they can validate their CAD analysis w ith complementary CAE calculations in cases where it is difficulties to understand the impact of a design concept.
Chalmers w ill include and further develop the tw o proposed procedures in ongoing research projects in the area.
The exchange betw een the parties have taken place in several stages. First, staff from Ziegler visited Volvo Cars where training in the CAE-based method E-line has conducted at Volvo Cars simulation environment. As a second step, Volvo Cars technical specialist w ithin squeak and rattle visited Ziegler to be trained in the CAD method Contact Point Analysis. The last step, 4 persons from Volvo Cars and one person from Chalmers visited Ziegler to be trained in the Contact Point analysis method. The cooperation betw een the parties w ill continue outside of the mobility project.
2015 – 2016
2017 – 2018
2013 – 2017
2015 – 2018
2017 – 2018
2017 – 2018
2017 – 2020
2015 – 2016
2017 – 2019
2017 – 2018
2017 – 2018
2015 – 2016
2014 – 2017
2015 – 2016
2016 – 2016
2017 – 2018
2016 – 2016
2017 – 2018
2014 – 2017
2016 – 2019
2016 – 2016
Tooling constitutes a significant part in the economical investment of the hot stamping process. Significant benefits in production economy and environmental benefits can be attained by improving the tribological performance in hot forming operations of automotive components. The main idea of this project is to create tailored tool surfaces on dies made from cheaper and easier to manufacture tool steel for the hot stamping of ultra-high strength steels.
2015 – 2018
2016 – 2016
2015 – 2015
The project focuses on economic and environmental sustainability and increased industrial competitiveness.
2017 – 2018
2017 – 2018
2016 – 2018
2017 – 2021
2014 – 2017
2014 – 2017
With globalization and other megatrends as demographic changes and climate change, more knowledge is needed regarding production in an international perspective. PADOK Study Visit in India 2016 have given an increased knowledge regarding how production is conducted in India, some of the challenges producing companies in that region is facing and how Swedish companies interested in investing in production in India could act to establish themselves in the region.
2016 – 2016
2016 – 2017
2015 – 2016
2015 – 2016
2014 – 2017
Reduced lead times and improved performance for tooling through innovative manufacturing and assembly strategies as well as optimised design enabled by use of additive manufacturing (AM).
2016 – 2018
2015 – 2017
2017 – 2018
2015 – 2016
2015 – 2016
2014 – 2018
2017 – 2020
Increased sustainability and cost effectiveness through improved strategic decision-making in production issues based on new metrics system for production and development.
2015 – 2017
2015 – 2015
The SAPPA project is about innovative cloud-based predictive and preventive maintenance systems, improving availability of products and production systems.
2014 – 2016
2013 – 2017
2014 – 2014
2013 – 2016
2016 – 2017
2016 – 2018
2014 – 2016
2015 – 2016
2014 – 2017
2013 – 2016
2015 – 2016
Every manufacturing company measure and control production performance with a system of KPIs. The aim of the SMART-PM project is to investigate and demonstrate new ways of collecting data, transforming data to information and introducing new decision tools based on valid information and economic models of the production systems.
2018 – 2020
RemProLife aims at improving the use of life-cycle information to achieve more efficient remanufacturing from economic and ecological perpectives.
2013 – 2016