Åsa Fast-Berglund
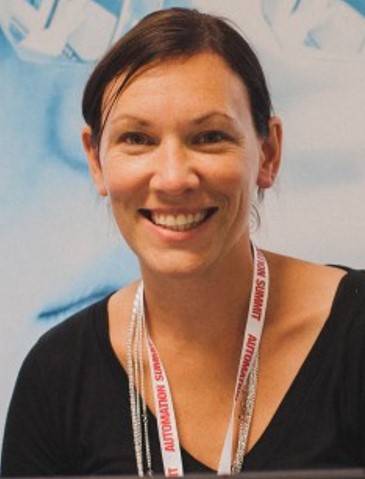
Project time: 2017 – 2020
Budget: 19 183 000 kr
Funding: SIP Produktion2030
The project will evaluate and validate new user-adapted and digital solutions for information sharing, work instructions, and resource planning in manufacturing contexts. An existing testbed environment, Chalmers Smart Industry Lab, will be utilized by the consortium to test increased efficiency and flexibility of implemented information and production systems.
Expected industrial impacts are e.g. reduced cycle-time; operator empowerment; reduced time from idea to implementation of digital solutions integrating hard- and software solutions.
The different strategies and technologies for digitalisation will be tested in the lab as a first step, in pilot plant with company adjustments as a second step and the final step will be to test the chosen solutions within the production environment. The demonstrators in each projects will also be used for education for a broader range of companies outside the consortium and also for education of engineers at Chalmers.
2015 – 2016
2014 – 2017
2015 – 2016
2016 – 2018
The project focuses on economic and environmental sustainability and increased industrial competitiveness.
2017 – 2018
2015 – 2015
2014 – 2018
2015 – 2016
Increased sustainability and cost effectiveness through improved strategic decision-making in production issues based on new metrics system for production and development.
2015 – 2017
2014 – 2016
2015 – 2016
2014 – 2017
2017 – 2018
2016 – 2016
With globalization and other megatrends as demographic changes and climate change, more knowledge is needed regarding production in an international perspective. PADOK Study Visit in India 2016 have given an increased knowledge regarding how production is conducted in India, some of the challenges producing companies in that region is facing and how Swedish companies interested in investing in production in India could act to establish themselves in the region.
2016 – 2016
2015 – 2018
Tooling constitutes a significant part in the economical investment of the hot stamping process. Significant benefits in production economy and environmental benefits can be attained by improving the tribological performance in hot forming operations of automotive components. The main idea of this project is to create tailored tool surfaces on dies made from cheaper and easier to manufacture tool steel for the hot stamping of ultra-high strength steels.
2015 – 2018
2017 – 2018
RemProLife aims at improving the use of life-cycle information to achieve more efficient remanufacturing from economic and ecological perpectives.
2013 – 2016
2015 – 2016
Reduced lead times and improved performance for tooling through innovative manufacturing and assembly strategies as well as optimised design enabled by use of additive manufacturing (AM).
2016 – 2018
2017 – 2019
2014 – 2017
2016 – 2017
2016 – 2019
2017 – 2018
2016 – 2018
2017 – 2018
2014 – 2014
2017 – 2018
2014 – 2017
2015 – 2015
2015 – 2016
2017 – 2020
2014 – 2017
2016 – 2016
2013 – 2016
2015 – 2016
Every manufacturing company measure and control production performance with a system of KPIs. The aim of the SMART-PM project is to investigate and demonstrate new ways of collecting data, transforming data to information and introducing new decision tools based on valid information and economic models of the production systems.
2018 – 2020
2015 – 2016
2015 – 2016
2015 – 2017
2013 – 2016
The SAPPA project is about innovative cloud-based predictive and preventive maintenance systems, improving availability of products and production systems.
2014 – 2016
2013 – 2017
2016 – 2016
2013 – 2017
2015 – 2016
2017 – 2021
2016 – 2016
2017 – 2018
2017 – 2018
2015 – 2016
2017 – 2018
2014 – 2017
2016 – 2017
2017 – 2018