Cecilia Groth
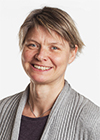
Project time: 2017 – 2020
Budget: 12 789 000 kronor
Funding: SIP Produktion2030
Digi-load focuses on to enhance the competitiveness in the Swedish surface treatment industry through automation and digitalization
Digi-load focuses on to enhance the competitiveness in the Swedish surface treatment industry through automation and digitalization. In Sweden there are around 400 surface treatment companies, job-coaters and in-house painting companies, with a large proportion of SMEs. The industry is in fierce competition from low-wage countries and many moved their production abroad. By increasing the automation and digitalization of the industry in the most labor demanding processes (up to 60% of production staff), the loading and un-loading of products, the competitiveness can be increased. In the project, existing test sites, physical and virtual, will use technologies (traditional and collaborative robots combined w ith vision and sensor technologies), focusing on demonstrating today’s and tomorrow ‘s possibilities of automation and digitization in the areas of loading and un-loading products. The processes require a big flexibility as a company can have up to 2000 different products to handle.
The testbed is located at the following sites:
1) Robotdalen – Mälardalen University and ABB’s testing center for automation, focus is on traditional robots combined with vision and sensor technology
2) Paint Center (Swerea IVF) – Collaborative Robots for loading/un-loading components, mostly small components in large series
3) IPS (FCC) – Virtual test site focusing on simulation, optimization and digital twins.
4) MIBA Industriteknik – Industrial demonstrations
The consortium includes automation companies, hook, conveyor, robot suppliers, job-coaters and in-house painting companies and research organizations.
To lay the foundation for tomorrow’s network of circular economy microfactories producing products designed by Swedish industry and produced from local recycled plastics.
2022 – 2023
The aim of the present project is to develop a prediction tool for laminated veneer products (LVPs) to make it possible for the industry to improve product performance by reducing rejects and customer complaints and reducing time from idea to market by means of a tool to simulate LVP performance.
2019 – 2021
Implementation of thin film pre-treatments to replace ZnPh for a more sustainable and cost-efficient production.
2019 – 2022
The project created a sustainable test bed that by provides Swedish industry with facilities and tools to physically and virtually evaluate different manufacturing concepts.
2013 – 2016
Tidsättning av manuell montering är centralt för verkstadsindustrins konkurrenskraft.
2021 – 2024
SCARCE II will develop a demonstrator to show how SMEs and associated value flows can increase efficiency, competitiveness, sustainability and internal collaboration through digitalisation. The goal is to show the value of a new digital solution. SCARCE focuses on two subcontractors in the value chain linked to Scania and Volvo. The demonstrator is a cloud-based solution that connects three test beds in the industry; Stena Industry Innovation Lab, Chalmers, RISE IVF lab, Mölndal and KTH's test bed in Södertälje with the help of Siemens, AFRY, Qbim, Virtual Manufacturing and EQPack.
2020 – 2022
Novel methods, techniques and software for simulation of electrodeposition and galvanization processes.
2020 – 2023
The aim of the ARR project is to develop the potential of automation in repairs and remanufacturing
2018 – 2021
Demonstrating the effectivity of laser texturing before thermal spraying in an industrial environment
2021 – 2024
Knowledge is needed that can support design and control of automation in material handling systems.
2019 – 2022
A research collaboration between Luleå University of Technology and the company RGS 90 will provide new treatment methods for three common but problematic types of waste.
2015 – 2019
The project's goal is to assist industry enabling sustainable work for operators during assembly of wire harnesses.
2022 – 2025
Maintenance in existing plants is becoming increasingly important, where predictive maintenance has become an emerging technology. The use of decision support tools contributes to environmentally and economically sustainable production. Within this project, different types of digital twins have been designed and evaluated. Specifically, new predictive model types have been tested in two different industrial case studies; a heat exchanger at SSAB and a profiled header at Svenska Fönster AB.
2017 – 2018
Methods for 3D scanned digital twins for efficient development and installation of production facilities at SMEs
2018 – 2021
MIDWEST will develop mechanisation solutions for Post-weld treatment methods of welded components.
2020 – 2023
The paintshop is often a bottleneck in production and the processes are fine-tuned based on testing on numerous prototypes. To meet the future demands there is a great need to improve the product preparation process. The aim is to develop methods, techniques and software, and supporting measurement methodology, for simulation of paint curing in IR and convective ovens. The goal is to assist the industry to further develop and optimize their surface treatment to be more energy and cost efficient; to have a shorter lead time in product development; and to give a higher product quality.
2016 – 2019
The project aims at radically improving the working environment and the employee security within the heavy manufacturing industries by using and adapting the latest technology for low and ultraprecise positioning and decision support systems. The target is to increase security and safety by adapting the decision-support and positioning system for the heavy manufacturing industries.
2017 – 2018
The goal is to increase the knowledge in robust design and manufacturing of components with high quality and low environmental impact.
2018 – 2020
To demonstrate the new technology with robots that enable Swedish companies to develop innovative new products for automated production o maintenance.
2017 – 2020