Boel Wadman
Phys. Dr
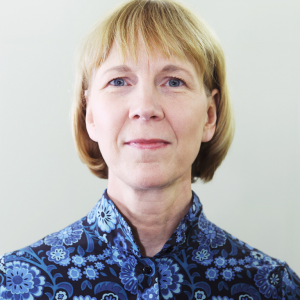
Project time: 2013 – 2016
Budget: 10 652 000 SEK
Funding: SIP Produktion2030
The project created a sustainable test bed that by provides Swedish industry with facilities and tools to physically and virtually evaluate different manufacturing concepts.
Project aim and objectives
The project aimed to create a sustainable test bed that strengthens Swedish industry by providing facilities and tools to physically and virtually test and evaluate different manufacturing concepts. This has been achieved. Furthermore, cooperation with SMEs has been established for efficient interactions that enable companies and students to actively exploit the test beds even after the project.
Results and expected impact
The project has delivered results in several categories: 1) Direct benefit to the project partner industries through their pilot cases 2) Generic knowledge concerning cooperation with SMEs in different concept phases 3) Strengthened networking within manufacturing
As a concrete outcome of the project, four new products were developed, two of which have reached the market.
Methods and analysis
Four small and medium-sized companies with proprietary products have acted as partners with their own industrial cases in the test bed development and have been interviewed about the collaboration and future needs.
Technology transfer has taken place via conferences and exhibitions, where prototypes developed in the partner companies were demonstrated. An important part of the test bed was the network created, and the cross-functional teams of researchers, companies and external experts who worked on the pilot cases. Through international collaboration the test bed has been linked to three EU applications, of which one is approved, and another is KIC Added Value Manufacturing. The ground work for collaboration among the project partners for upcoming European and national projects has been established.
Målet var att förstå de utmaningar som den svenska och japanska industrin står inför studiebesök.
2017 – 2018
The goal is to increase the knowledge in robust design and manufacturing of components with high quality and low environmental impact.
2018 – 2020
Urinary incontinence is a common problem that affects everyone, ranging from young women who have recently given birth to men who have undergone prostate surgery. Amongst people over the age of 70, almost half of everyone, both women and men, suffer from involuntary urine leakage.
2021 – 2023
Tidsättning av manuell montering är centralt för verkstadsindustrins konkurrenskraft.
2021 – 2024
A large number of building boards are used in both construction and furniture manufacturing. They are usually made of sawdust with a formaldehyde-based adhesive as a binder. However, they have some problems, including the fact that shavings absorb moisture and that formaldehyde is both allergenic and potentially carcinogenic. The LigniGC project aims to develop a better alternative.
2021 – 2023
Cyclicor, which has its origins at Lund University, has in a previous project within Mistra Innovation successfully developed a method for producing the plastics polycarbonate (PC) and polyurethane (PU) without toxic additives. One goal of the Polyfree 2.0 project is to increase the production of the new plastics from lab scale to quantities that enable the participating industrial companies in turn to take steps towards finished products. Other goals are for the plastics to be recyclable as well as have the required properties.
2021 – 2023
Novel methods, techniques and software for simulation of electrodeposition and galvanization processes.
2020 – 2023
TriBlade is a new ground-breaking technology for rotor blades in wind turbines, which have the potential to affect the entire wind power market. The technology has been developed by Winfoor in collaboration with Lund University and is based on each rotor blade designed as a truss.
2015 – 2019
Indium is a silvery metal that is very soft and malleable. Together with tin, the metal can be used to create indium tin oxide with properties that make it one of the most important components in the electronics industry. The goal of the project is therefore to build a recycling unit in a continuous production without waste.
2021 – 2023
Failure prediction for complex load cases in sheet metal forming
2020 – 2023
The aim of the present project is to develop a prediction tool for laminated veneer products (LVPs) to make it possible for the industry to improve product performance by reducing rejects and customer complaints and reducing time from idea to market by means of a tool to simulate LVP performance.
2019 – 2021
Digi-load focuses on to enhance the competitiveness in the Swedish surface treatment industry through automation and digitalization
2017 – 2020
For more than a hundred years, lubricants for various types of machines have mainly been made from fossil oil. The function has improved over time, but they also have disadvantages; they negatively affect the environment, human health and the climate. The project will therefore work to improve the practical applications by, together with other tests, combining lab tests with field tests.
2021 – 2023
The paintshop is often a bottleneck in production and the processes are fine-tuned based on testing on numerous prototypes. To meet the future demands there is a great need to improve the product preparation process. The aim is to develop methods, techniques and software, and supporting measurement methodology, for simulation of paint curing in IR and convective ovens. The goal is to assist the industry to further develop and optimize their surface treatment to be more energy and cost efficient; to have a shorter lead time in product development; and to give a higher product quality.
2016 – 2019
The SQID project will develop an industrial cleaning and drying machine using Qlean water instead of traditional chemicals.
2016 – 2018
A new environmentally friendly process for production of graphene based on equipment normally used in pulp industry
2021 – 2021
Methods for 3D scanned digital twins for efficient development and installation of production facilities at SMEs
2018 – 2021
Urinary incontinence is a common problem that affects everyone from young women who have recently given birth to men who have undergone prostate surgery. Amongst people over the age of 70, almost half of everyone, both women and men, suffer from involuntary urinary leakage.
2021 – 2023
A research collaboration between Luleå University of Technology and the company RGS 90 will provide new treatment methods for three common but problematic types of waste.
2015 – 2019
To lay the foundation for tomorrow’s network of circular economy microfactories producing products designed by Swedish industry and produced from local recycled plastics.
2022 – 2023
Resilient and sustainable production for proactive production development of greenfield/brownfield.
2021 – 2024