Lars Blomqvist
Ph.D. in Forest Industry Production Systems
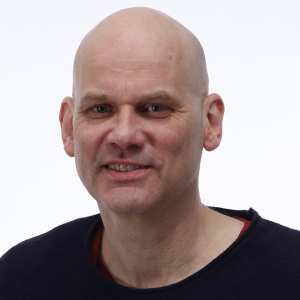
Project time: 2019 – 2021
Budget: 6 697 936 kronor
Funding: SIP Produktion2030
The aim of the present project is to develop a prediction tool for laminated veneer products (LVPs) to make it possible for the industry to improve product performance by reducing rejects and customer complaints and reducing time from idea to market by means of a tool to simulate LVP performance.
When a deviation from the intended shape occurs, it poses a major problem for both manufacturers and customers. There is a lot of money to earn and resources to save for the producers and users of LVPs if rejects of LVPs could be reduced. During moulding of LVPs the veneers are exposed to moisture-related stresses and a significant mechanical compression of the thickness. Previous surveys have indicated that the surface pressure during moulding is often uneven, which may affect the shape stability and strength of the final product.
To obtain a reliable statistical basis tests will be performed on several small samples. The test results will be used for validation and development of a simulation model of LVPs. The focus of tests are to study both mechanical and structural properties at different times during the curing process and relate them to the cell structure properties of the wood material. The test samples are a variety of selected configurations of LVP moulded in real life to provide the experimental basis for validation of performance of the corresponding virtual product.
The goal is to increase the knowledge in robust design and manufacturing of components with high quality and low environmental impact.
2018 – 2020
The project resulted in a supportive tool for collaboration projects with the purpose of developing robust production equipment with high production efficiency in combination with low operational and maintenance costs.
2013 – 2016
A new environmentally friendly process for production of graphene based on equipment normally used in pulp industry
2021 – 2021
Investigate the preconditions for services on digitalized geometrical metrology. E.g. Mentoring coordination
2018 – 2019
The overall goal of DiSAM is to create a unique test AM Hub in Sweden for metal and polymer based additive manufacturing processes.
2017 – 2021
The project created a sustainable test bed that by provides Swedish industry with facilities and tools to physically and virtually evaluate different manufacturing concepts.
2013 – 2016
Novel methods, techniques and software for simulation of electrodeposition and galvanization processes.
2020 – 2023
Building systems for timber structures, which reduces construction cost and climate impact.
2021 – 2024
To lay the foundation for tomorrow’s network of circular economy microfactories producing products designed by Swedish industry and produced from local recycled plastics.
2022 – 2023
Difficulties in joining are often a limiting factor for vehicle manufacturers during product weight reduction.
2020 – 2023
The paintshop is often a bottleneck in production and the processes are fine-tuned based on testing on numerous prototypes. To meet the future demands there is a great need to improve the product preparation process. The aim is to develop methods, techniques and software, and supporting measurement methodology, for simulation of paint curing in IR and convective ovens. The goal is to assist the industry to further develop and optimize their surface treatment to be more energy and cost efficient; to have a shorter lead time in product development; and to give a higher product quality.
2016 – 2019
Innofacture är en Företagsforskarskola som bedrivs i samverkan mellan Mälardalens högskola och tio av landets största tillverkningsföretag. Projektet fokuserar både på innovation och produktion för att utveckla produktionsprocesser i företagen.
2012 – 2021
Digi-load focuses on to enhance the competitiveness in the Swedish surface treatment industry through automation and digitalization
2017 – 2020
Better work instructions for more efficient and inclusive work
2022 – 2025
Tidsättning av manuell montering är centralt för verkstadsindustrins konkurrenskraft.
2021 – 2024