Evelina Styhre
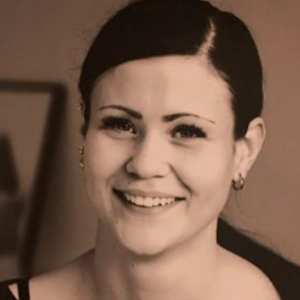
Urinary incontinence is a common problem that affects everyone, ranging from young women who have recently given birth to men who have undergone prostate surgery. Amongst people over the age of 70, almost half of everyone, both women and men, suffer from involuntary urine leakage.
To alleviate the problem, which can be socially stigmatizing, different types of protection are used. These are usually disposable due to the fact that the reusable variants available today do not have the same function or convenience as the disposable alternatives.
From an environmental perspective, however, it is important to be able to shift the consumption of disposable products to more circular solutions, something that the health care system also demands.
One challenge is to get users, who are often ashamed of their problems, to want to use washable protection. Explanations for this are that it is both easier and more discreet to use something that can be thrown away after use, and that the washable alternatives available today are not able to absorb and retain liquid as well as disposable protection that contains effective superabsorbents.
In order to develop well-functioning reusable incontinence guards, the ReusableUP project will explore liquid dispersion in textile materials. One question which will be answered is how to best achieve optimal liquid handling in composites with several textile layers by combining different fibers, yarns and textile structures. Another is to investigate which parameters optimize permeability, dispersion and absorption of liquid in and between different layers.
It is simply a matter of obtaining a protection where liquid is quickly absorbed in the upper layers, and then distributed and absorbed in the underlying layers without penetrating to the surface again. It is also important to deal with the contradiction that exists between good function and washability. Not least because the properties that make a protection effective should not disappear when the material is washed.
The final goal of the project is to develop a prototype of a reusable protection adapted for mild to moderate urinary incontinence in order to be able to perform user tests.
This project is run in collaboration with the University of Borås, Facilette and Sanicare AB.
The SQID project will develop an industrial cleaning and drying machine using Qlean water instead of traditional chemicals.
2016 – 2018
The project aims to improve the collection system for recycling of pre-consumer plastic waste.
2022 – 2023
A new environmentally friendly process for production of graphene based on equipment normally used in pulp industry
2021 – 2021
The project aims to test the idea of an effective circulation system for material waste from additive manufacturing. Our goal is to map the prerequisites for closer collaboration between material suppliers and additive manufacturers, including new business models, partnerships and logistics solutions.
2017 – 2018
Urinary incontinence is a common problem that affects everyone from young women who have recently given birth to men who have undergone prostate surgery. Amongst people over the age of 70, almost half of everyone, both women and men, suffer from involuntary urinary leakage.
2021 – 2023
For more than a hundred years, lubricants for various types of machines have mainly been made from fossil oil. The function has improved over time, but they also have disadvantages; they negatively affect the environment, human health and the climate. The project will therefore work to improve the practical applications by, together with other tests, combining lab tests with field tests.
2021 – 2023
Reduced variation in machinability promote lower costs, predictable and a sustainable processing of grey cast iron components.
2020 – 2022
The project created a sustainable test bed that by provides Swedish industry with facilities and tools to physically and virtually evaluate different manufacturing concepts.
2013 – 2016
Failure prediction for complex load cases in sheet metal forming
2020 – 2023
The project's goal is the circular use of plastic in cars through reuse and recycling.
2023 – 2025
Today, the industry often uses energy- and time-consuming autoclave processes for the manufacture of composites with high quality requirements, towards for example the aerospace industry.
2017 – 2018
Resilient and sustainable production for proactive production development of greenfield/brownfield.
2021 – 2024
To lay the foundation for tomorrow’s network of circular economy microfactories producing products designed by Swedish industry and produced from local recycled plastics.
2022 – 2023
A large number of building boards are used in both construction and furniture manufacturing. They are usually made of sawdust with a formaldehyde-based adhesive as a binder. However, they have some problems, including the fact that shavings absorb moisture and that formaldehyde is both allergenic and potentially carcinogenic. The LigniGC project aims to develop a better alternative.
2021 – 2023
A research collaboration between Luleå University of Technology and the company RGS 90 will provide new treatment methods for three common but problematic types of waste.
2015 – 2019
Cyclicor, which has its origins at Lund University, has in a previous project within Mistra Innovation successfully developed a method for producing the plastics polycarbonate (PC) and polyurethane (PU) without toxic additives. One goal of the Polyfree 2.0 project is to increase the production of the new plastics from lab scale to quantities that enable the participating industrial companies in turn to take steps towards finished products. Other goals are for the plastics to be recyclable as well as have the required properties.
2021 – 2023
Indium is a silvery metal that is very soft and malleable. Together with tin, the metal can be used to create indium tin oxide with properties that make it one of the most important components in the electronics industry. The goal of the project is therefore to build a recycling unit in a continuous production without waste.
2021 – 2023
Målet var att förstå de utmaningar som den svenska och japanska industrin står inför studiebesök.
2017 – 2018
Reduce the environmental impact of foundries by reducing the amount of sand waste using machine learning.
2023 – 2024
The REWIND project combines the principles of lean production and eco-efficiency in three industry pilots at Stena Recycling, Volvo AB and IKEA GreenTech. The objective is to retain the value embedded in materials with circular strategies (reuse, remanufacture, recycle, repurpose, etc.). Lessons learnt from the pilots will be used to develop educational tools for engineers and industry leaders to accelerate the uptake of best practices for circularity and sustainable production.
2019 – 2022