Mélanie Despeisse
Associate Professor, Sustainable Manufacturing
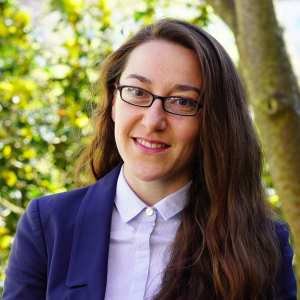
Project time: 2022 – 2023
Budget: 1 600 000 sek
Funding: SIP Produktion2030
Measure environmental performance and improve towards eco-efficient, climate-friendly and circular production
Manufacturing companies must implement greener practices to further contribute to sustainable development using approaches such eco-efficiency and circular economy, i.e. creating social and economic value while minimising the environmental impact of production through efficient, closed-loop circulation of resources. The project uses industrial digitalisation as an enabler to measure manufacturing systems’ environmental performance more holistically and support continuous improvements towards eco-efficient, climate-friendly and circular production systems. The operating principles are: reduce material and energy intensity (increase efficiency and eliminate or minimize waste), reduce toxicity (eliminate or minimize environmental impacts), increase sustainable use of renewable sources (for both energy and materials), retain value (circular strategies for product life extension and material waste valorisation) and increase service intensity (product-service systems and industrial services). To achieve the objective of FREED, we will focus on digital solutions for environmental sustainability at factory level. The feasibility study will review current practices and systems in place at the partners’ manufacturing sites to evaluate the applicability of various environmental tools, methods, and indicators. Core activities will include process mapping, data inventory, maturity assessments, and gap analysis to identify existing strengths and define areas of improvement to boost the environmental performance of production systems.
Roundtables with governmental organizations and industry regarding circular economy and product related legislation
2020 – 2021
Developing circular production systems using digital technologies
2021 – 2024
The REWIND project combines the principles of lean production and eco-efficiency in three industry pilots at Stena Recycling, Volvo AB and IKEA GreenTech. The objective is to retain the value embedded in materials with circular strategies (reuse, remanufacture, recycle, repurpose, etc.). Lessons learnt from the pilots will be used to develop educational tools for engineers and industry leaders to accelerate the uptake of best practices for circularity and sustainable production.
2019 – 2022
To lay the foundation for tomorrow’s network of circular economy microfactories producing products designed by Swedish industry and produced from local recycled plastics.
2022 – 2023
To create an inventory of AI techniques for maintenance services, apply AI techniques to three industrial cases, and evaluate their economic and environmental implications.
2017 – 2019
SE:Kond2Life - Ecosystem for reuse of automotive components
2019 – 2022
The project objective is to lay a foundation to develop a digital platform that can enable generating materials passports for products to facilitate implementation of Circular Production Systems.
2019 – 2019
SCARCE will investigate the needs, possibilities and obstacles in value chains up- and down-stream from a focal SME company. SCARCE will explore what data to measure and visualize, and how this data can enable more automated execution, as well as, more dynamic and proactive planning of production capacity and material flows across the companies in the value chain. In addition, we will study organizational capabilities, especially the future human role, for implementing and managing in a digital and data-driven value chain.
2019 – 2019
SCARCE II will develop a demonstrator to show how SMEs and associated value flows can increase efficiency, competitiveness, sustainability and internal collaboration through digitalisation. The goal is to show the value of a new digital solution. SCARCE focuses on two subcontractors in the value chain linked to Scania and Volvo. The demonstrator is a cloud-based solution that connects three test beds in the industry; Stena Industry Innovation Lab, Chalmers, RISE IVF lab, Mölndal and KTH's test bed in Södertälje with the help of Siemens, AFRY, Qbim, Virtual Manufacturing and EQPack.
2020 – 2022