Alexander Kaplan
Chaired Professor in Manufacturing Systems Engineering, Ph.D. in laser welding (Doktor techn.), MSc in Electrical Engineering (Dipl.Ing.)
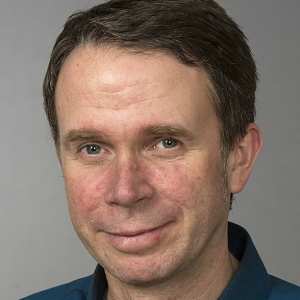
Project time: 2011 – 2014
Budget: 2 800 000 SEK
Laser Arc Hybrid Welding (LAHW), a combination of laser and arc welding, offers
higher productivity compared to traditional welding techniques like arc welding. This is
achieved by higher welding speeds and more advanced construction possibilities. Thus
far, laser arc hybrid welding is not used in the Swedish engineering industry but there are
already more than hundred installations worldwide. Scania has the ambition to implement
laser hybrid arc welding, but development of a robust process and increased
understanding of the weld during fatigue situations, especially concerning the weld upper
geometry, are required.
The robustness of the process was studied with a new fully controlled and systematic
traceability of tolerance. This is achieved by mapping parameters, measuring and
studying edge variations from the forming, and creating an understanding of its impact
upon the final weld by High Speed Imaging (HSI). Also the new arc welding process
CMT (Cold Metal Transfer) was studied in combination with laser beam welding. During
the project, sample workpieces and full-scale automotive components where welded with
LAHW with respect to process robustness, coupled quality control and fatigue behavior.
Basic differences between three arc welding processes (Cold Metal Transfer – CMT,
Pulsed, Standard) are investigated for each process function and process stability.
Tolerance windows for the weld joint types that occur on the demonstrator are
investigated and mapped for LAHW with CMT, as a technique for thick sheet metal
products. The new systematic measurement method (pre-, post-scanning and HSI) has
been further developed and applied on a complex automotive product. For a truck beamer
all the twelve weld sections has been mapped and optimized. From the results, six journal
and four conference papers has been produced and presented.
A new project (EU-FP7, HYBRO) continues where ROBUHYB ends. The HYBRO
project continues with the same demonstrator and therefore works as an extension of
ROBUHYB. It was prioritized to put more time to compare different techniques to get
even better results. Within HYBRO there also are a 6 m long demonstrator from a French
automotive company and two other Scania applications that are going to be investigated.
Besides that, HYBRO is a good opportunity to collaborate with world leading partners
that applies the new LAHW technique for high strength steels. Eight beamers have
already been 3D-robot welded at LTU in a fixture made by Ferruform (Scania).
Optimization of the demonstrator beamer welding continued when eight additional
beamers where first tack-welded at LTU and later welded at Fronius (Austria, leading
supplier of laser welding equipment) where additional errors were detected and therefore
avoidable.
The whole chain from construction (production development in Södertälje) and
material choice, cutting/forming, welding, finishing etc. (Ferruform in Luleå) was
analyzed from an economic and practical point of view, in order to prepare introduction
of LAHW in production.
The project will develop design solutions where existing/modified joining techniques are used for joining of new lightweight materials to more traditional materials
2016 – 2019
Validate previously developed failure models on component level. Implement models into a commercial code. Shorten lead time for new advanced components. 15 % weight reduction.
2015 – 2018
The paintshop is often a bottleneck in production and the processes are fine-tuned based on testing on numerous prototypes. To meet the future demands there is a great need to improve the product preparation process. The aim is to develop methods, techniques and software, and supporting measurement methodology, for simulation of paint curing in IR and convective ovens. The goal is to assist the industry to further develop and optimize their surface treatment to be more energy and cost efficient; to have a shorter lead time in product development; and to give a higher product quality.
2016 – 2019
2009 – 2011
The project’s objective has been to produce instructions, calculation models and other tools to facilitate optimized construction and production of screw joints.
2009 – 2011
This project aims to assess easier and cheaper quality assurance of spotwelded joints by controlling the electrode indentation.
2016 – 2017
All manufacturing processes are afflicted by variation which may violate the fulfilment of assembly requirements, functional requirements or esthetical requirements. Another issue is the difficulties to reach desired form in all areas.
2009 – 2013
The project aims to increase the knowledge about the mechanisms controlling the polishability of coated surfaces to facilitate the development and implementation phase of new and more environmental friendly coating systems.
2016 – 2019
2009 – 2013
2014 – 2014
An effective process can be realized only if there is a mechanism that facilitates information exchange and reuse of models and knowledge.
2009 – 2013
In material handling processes, such as kitting and sequencing, which are used in the automotive industry to supply the assembly with a wide and growing range of component variants, the picking information system is central design aspect. Given the developments in digitization, the purpose of this concept study is to evaluate the potential of digital technology to support materials handling work in production systems.
2017 – 2017
2010 – 2011
The project results show that it is possible to accurately simulate spray painting of a truck cab or a car in only a few hours on a standard computer.
2009 – 2012
In this projectthree areas of component realization are covered: casting, heat treatment and machining.
2009 – 2012
The project has addressed challenges in casting and realisation of new cast irons with improved properties and machinability, decision making regarding manufacturing strategies and machinability of materials. Silicon-alloyed compacted graphite iron (CGI) has been demonstrated av new alternative for future engine components. New simulation technique for assessing manufacturing strategies has been introduced. Generic know ledge has been developed w hen it concerns w ork material machinability w ith specific reference to combined materials in advanced components.
2012 – 2015
The project intends to translate the new information into improved procedures and processes in the automotive industry
2012 – 2014
In this project, we focus on two methods to make gears more high-strength, namely to replace gear milling with gear rolling based on plastic forming and the introduction of clean steels with reduced inclusion content
2012 – 2015
Our hypothesis is that advanced, lightweight, multi-layer-structured composites with good barrier properties and tailored biodegradability can be produced by combining bio-based thermoplastic with special additives and pulp fiber mats. This material is free from fossil raw materials, sustainable, fire and impact-resistant and suitable for interior components in vehicles.
2012 – 2013
The project LISA2 will deliver industrial-ready services enabling Swedish industry to understand and tune their factories
2015 – 2018
The aim was to identify the potential of a new production method where components are produced by partial forging of ductile cast iron.
2013 – 2014
The Hotform Project set out to obtain robust physical data on the hot forming process for use in improving the quality of finite element simulations used in the design and verification of parts and tooling for manufacturing press hardened auto body components
2012 – 2014
This project is part 2 of the PhD project "Modelling and simulation of simultaneous forming and quenching of Boron steel" funded by VINNOVA.
2008 – 2012
2009 – 2012
"Geometry Optimised adhesive joining for sustainable production” in Swedish (Geometri Optimerad LimFogning för hållbar produktion, "GOLF") is a project within the Swedish research program FFI for Sustainable production. It has as its mission to develop technology and methods to get the right amount of adhesive on the right place. The drivers behind this are the overall strive to decrease weight in vehicles and moving machines to minimize the amount of CO2 in the atmosphere.
2013 – 2015
The aim of the project has been to create a stable, reliable and verified concept for hemming of lightweight structures in multi-material, including virtual tools to determine sealed joints. This also ensures the quality costs since corrosion will not occur and thus facilitated the introduction of new lightweight materials.
2014 – 2017
To improve accuracy and usability for simulation of compression moulding through two PhD-students focusing on long and short fibre composites.
2017 – 2019
Protecting key competence in a global business environment requires control of intellectual properties (IP). The project will test how to specify the manufacturing of a product (Know how) without revealing the product IP (Know why).
2012 – 2013
2013 – 2017
The purpose of this project is to adopt and to demonstrate a system for automatic inspection of all manufactured components in-line in a production line.
2017 – 2020
The proposed project aimed to implement the digital human modelling tool IMMA in Swedish industry and universities.
2013 – 2016
The objective was to test strength, stiffness, production cycle time and cost for the rear end of a Volvo city bus using 3Dlitetechnology.The result is that the technology functions and that the the production cycle time is about 3 min for the core filling.The design has been compared with a carbon fiber structure and is as strong and stiff as the carbon fiber structure but to much lower cost.
2013 – 2014
There is an urgent need for Swedish industry to explore strategies and methods to accelerate the efficiency progress and support decision making in order to regain profitability.
2009 – 2012
2011 – 2013
The surface treatment is the process in an automotive factory that consumes most energy, water and chemicals, and produces most waste and pollution
2012 – 2015
The project aims to develop a new type of abhesion multilayer system based on the combination of layers with different mechanical/physical properties that can provide customized features for wear, friction, adhesion and wettability
2012 – 2013
The integration of data management systems, simulation software and optimization algorithms have been shown to increase throughput in existing production but also allow expanded use of virtual tools in the preparation phases. This in turn leads to shorter development times for new production systems and products. The project has also contributed to greater understanding and concrete improvements in the processes of collecting and assure the quality of production data. This in turn increases the quality in both simulations and direct data-driven analyzes.
2013 – 2017
The aim of the project was to create 10 new modules for continuous education and training for professionals and students in undergraduate education.
2014 – 2016
We have built a Swedish Research Park for development and test of calibration processes for alcolock prototypes, aiming at a future high-volume production
2012 – 2014
The projects aim was to combine the technologies from virtualization to digitalize the methods from visualization in order to enable their usage in global teams as well as to create transparency between knowledge work and the management of the knowledge needed for the execution and improvement of that knowledge work
2012 – 2015
The project will develop a non-destructive testing method based on laser-ultrasonics (LUS) aiming for mechanized quality control of joints in industrial environments.
2014 – 2017
SIMET GICP has been a very successful research project and has resulted in a task model for the systematic measurement technology planning and preparation.
2009 – 2013
This project focuses on the development of a new generation of fasteners B14 with a significantly higher strength than the conventional fasteners 10.9 and 12.9 used today, i.e. the new fasteners have a target tensile strength higher than 1400 MPa combined meantime with satisfactory ductility
2011 – 2013
Robust laser welding of aluminium by using innovative laser welding tools and prediction models to avoid cracking and distortions
2017 – 2020
2009 – 2011
The project is mainly addressed to manufacturing of components and sustainable production engineering
2011 – 2012
2013 – 2015
The objective with this project is to develop a new innovative process technology for the press hardening process.
2009 – 2011
2013 – 2015
2012 – 2015
The purpose of this project is to bridge the gap betweenmechanical and electrical engineers in order to achieve a more efficient productionpreparation, enabling virtual commissioning and automatic generation of verified controlprograms.
2009 – 2012
The project has confirmed the hypothesis that tailoring of the tempering is a functioning means of making PM steel sustainable towards high static loading in potential automotive applications. The project has also developed further understanding about mechanisms that could be responsible for static loading sensitivity with respect to creep/relaxation at slightly elevated temperature. The results relate to sustainable manufacturing processes, the basis being that powder compaction and sintering is an energy efficient way with high raw materials utilization.
2012 – 2013
The overall objective of the project was to: • Develop simulation methodology for drive simulation of transmissions with given shape, surface topography and surface structure, - for more robust and better prediction of the efficiency and life of gear contacts in gearboxes. • Through experimental evaluation and characterization, support and verify the developed simulation technology • Through experimental evaluation and characterization, further verifying the potential of using the correct surface texture, e.g. honing, and right-handed gear in heavy-duty transmissions.
2016 – 2018
The project aimed to develop a concept for self-piercing riveting in material combinations that are not recommended to join together with self-piercing riveting. This is by using the so called “Plugg-concept”.
2013 – 2016
The project ALKOMP have addressed challenges with aluminum in sheet forming
2012 – 2015
2013 – 2014
Increased demands on an efficient and sustainable automotive industry, driven by international competition and global demands on reduced use of resources, requires more efficient manufacturing systems
2011 – 2013
2014 – 2017
2009 – 2013
The aim is to facilitate an increase in use of nitriding processes in order to create surfaces with high strength and friction and wear properties
2014 – 2017
This research project (ONWELD) serves to investigate and verify the potential for new laser scanning technologies and developed algorithms as a modern tool for automated, unbiased geometrical weld quality assurance.
2013 – 2016
Further development of solutions for powerful collaborative robots, focusing on safety issues and the use of an enabling device.
2015 – 2018
The press hardening process is based on the forming of hot blanks, in the austenitic state, to improve the formability as well as obtaining a final martensitic structure by subsequent rapid cooling in the forming tools
2010 – 2012
The combination of ultra high strength steels and aluminium is expected to play a large role in the vehicles of the future. In the project we test the hypothesis that friction stir welding can be used to create high performance joints.
2012 – 2013
2010 – 2012
The aim of the project is to investigate the synergies obtain by a holistic optimization framework that simultaneously optimize the product, the production system, and the manufacturing processes.
2012 – 2013
2013 – 2016
Develop innovative concepts for in-line NDT of heat treated components, hence minimizing the need for costly and time consuming destructive testing.
2015 – 2018
This project addresses challenges of sustainable manufacturing of high-added value powertrain components involving efficient and robust machining of advanced materials.
2009 – 2012
This project was using electromagnetic pulse power to develop a new unique innovative production process in the following area: Adiabatic cutting/shearing – The major benefit is the ability to create holes in steel sheet materials by single side punching holes.
2010 – 2012
The project is aimed at developing and testing a new principle for dynamic planning and preparation of assembly where balancing is optimized at a higher system level, considering assembly sections rather than stations, which is common today. This would entail significant savings since today’s view of the workstation concept creates a discrete, inflexible entity with balancing losses
2012 – 2013
2009 – 2012
Finding effective ways for skills and technology diffusion (K & TS ) of research and coordination of educational resources is a strategic area for Swedish industry to master. The need for training at all levels to cope with future products , materials and processes will increase.
2013 – 2014
The project goal is to minimize distortion of hardened components by evaluation and minimising effects from factors causing distortion potential in the process chain.
2015 – 2018
The hypothesis has been inspired by materials that consists of fibers can be more easily cut with a blade using wavy profile. The cutting motion is important, is it possible with the help of ultrasound to create a more favorable cutting motion.
2012 – 2013
Develop manufacturing technologies where composites are integrated directly to metals in production systems for press hardened boron steel and hot-formed aluminum.
2015 – 2016
OptiDies has created new, in-depth understanding of the prevailing complex tribo-systems when forming AHSS. Skills involved are tribology, sheet and tool steel, die manufacturing methods, numerical analysis and cost modelling.
2009 – 2012
The project objectives were to understand if atmospheric plasma could act as cleaning and activation process before bonding and allow for an implementation with a moderate investment cost of a process that is generic for a variety of applications.
2012 – 2013
This project enables more extensive utilization of virtual tools based on increased access to the manufacturing related data.
2009 – 2012
2014 – 2015
2014 – 2017
It is a key issue for the automotive manufacturing industry to sense, and to have the ability to act on changes on the market with respect to environmentally friendly and lightweight products
2011 – 2014
This hypothesis will investigate the potential of tooling solutions and other methods, considering demands from technology, business models and communication.
2012 – 2013
Syftet var resultatsspridning och detta uppfylldes verkligen med 104 högkvalitativa presentationer för industri
2011 – 2012
To develop methods and models for prediction of die conditions in press hardening
2014 – 2017
2014 – 2015
2009 – 2012
With globalization and other megatrends as demographic changes and climate change, more knowledge is needed regarding production in an international perspective. PADOK Study Visit in India 2016 have given an increased knowledge regarding how production is conducted in India, some of the challenges producing companies in that region is facing and how Swedish companies interested in investing in production in India could act to establish themselves in the region.
2016 – 2016
The hypothesis is that assembly of future light-weighted vehicles drastically will change the vehicle production process. The aim is to identify future production process and future research areas.
2012 – 2013
Flexible assembly for Considerable Environmental improvements of CAR's
2009 – 2012
The overall goal was to gain experience from a full-scale demonstrator in Saab´s paintshop with emphasis on energy saving in Swedish automotive paintshops. Paintshops are the largest consumers of energy in these factories
2011 – 2012
The objective has been to manufacture components with low friction and high wear properties and reduce the need for post machining and straightening by utilizing the full potential of nitriding processes in combination with selection of steel grade
2009 – 2013
The overall purpose of this project has been to demonstrate how a model-driven workflow can streamline process planning and quality assurance. Model-driven process planning and quality assurance has great potential to contribute to a significant productivity increase in process planning and quality assurance.
2014 – 2017
Increase competitiveness by developing complete work chain from virtual preparation, through automatically generated PLC code, to virtual and physical commissioning.
2014 – 2017
2012 – 2013
Gear transmission products are strategically important key components in powertrains produced by the Swedish automotive industry
2009 – 2012
The project goal was to create methods and tools for proactive assembly ergonomic and geometric quality assurance for sustainable production.
2013 – 2016
The project is based on the hypothesis that it is possible to establish measurable objective evaluation criteria of characteristics for joining in various combinations of materials.
2012 – 2013
The aim with the project is to test a new method to join thermoplastic composite to metal in a lap joint by using a focused TIG arc, as a heat source, to heat the metal side just enough so that the composite melts and join to the metal. The method gives single sided access, no need for additional filler material and makes invisible joints possible. The objective is to have a joining method that is robust, gives high productivity and high quality as well as cost advantages.
2012 – 2013
The project's main goal is to develop a design and manufacturing methodology, for resource efficient additive manufacturing of components in the automotive industry.
2017 – 2020
The project is expected to result in strengthening the Swedish automotive industry competitiveness and also to reduce the environmental impact from heavy duty vehicles.
2015 – 2016
This project will address some of the main obstacles in introducing FSW as a flexible joining process within vehicle production.
2009 – 2012
The manufacturing time of sintered steel components will be reduced by using induction sintering. The following surface hardening with induction aims at increasing the performance and therewith the possible applications.
2012 – 2013
2012 – 2015
2009 – 2013
The study includes a literature study, the test of different electrochemical solutions, and the design of a simplified setup for performing LECD. At the end of the feasibility study, sufficient knowledge should be achieved to evaluate if LECD can be a potential method for localized treatment in the context of re-manufacturing.
2015 – 2016
This project is aimed at developing competitive light weight steel solutions for the car body by reducing the density of the blank material without any major change in the elastic stiffness. The low density steel blank is a laminate (sandwich) with outer layers of ultra-high strength steel and low density core created by sintered metal powder.
2013 – 2016
The project has studied how the silanoles are affected by different treatments.
2013 – 2016
The project QScrew aims to create improved processes for the design, testing, validation and assembly of bolted joints.
2015 – 2017
By combining sheet metal forming technology with CRTM processes and highly reactive matrix material the goal are to reach same production rate as for sheet components
2012 – 2013
A study “before and after” EnviroMan, indicates that the project has created increased understanding on specific topics and also useful results
2012 – 2015
2017 – 2018
The project focuses on how to reduce waste/cost caused by environmental aspects and adding value to the production system by green strategies and actions
2009 – 2012
The following project aim to develop test routines for coating systems, in order to secure final surface quality when new coating systems are introduced in production
2013 – 2014
This research project has studied the influence on the accuracy of FE-predictions of springback in sheet metal forming from different material models
2010 – 2012
The objective is to evaluate the suitability of additive technology for creating possibilities for the use of new materials and new processing strategies in the production of lightweight components with high demands on product characteristics and reasonable production costs.
2012 – 2013
2011 – 2013
The main aim with the project was to create solutions that enable globalization of production by using smart ICT-tools.
2013 – 2015
The aim of Lightstruct is to develop conditions to manufacture lightweight welded structures within construction machineries
2012 – 2014
The goal of this project is faster product realizations of hybrids and fully electrified light weight vehicles by developing digital tools for efficient geometrical packing and assembly path planning and analysis of flexible parts.
2009 – 2013
Predictive process models for thermo-mechanical forming processes like press hardening have been developed during this project
2011 – 2014
The basic idea behind the project Additive Manufacturing of metal cutting tools was to utilise so called additive manufacturing technology to produce metal cutting tools used by the automotive industry to manufacture power transmission gears.
2013 – 2016
The project “Design of Materials Preparation Processes” deals with materials preparation as a means for the production system to manage the increasing numbers of component variants, which is an ever growing challenge in modern assembly operations.
2014 – 2017
Future sustainable competitive production systems need to be productive and flexible, as well as environmentally friendly and safe for the personnel
2011 – 2014
In this project, a pre-treatment of uncoated boron steel has been investigated, which after hot stamping results in the formation of an oxide showing excellent adhesion to the steel
2012 – 2014
To replace the manual inspection, minimize the consequences of defects and to improve the quality of delivered products with an efficient and automated Quality Control system.
2016 – 2019
The goal of the project was to implement a new quality system for welding in design and manufacturing of welded components
2010 – 2012
Operation planning systems based on standardised international and generic models for communication and interaction and which easily can be adapted to company needs will give great advantages.
2009 – 2013
2010 – 2011
The project goal is to test manufacturing of a 7 m bus side using 3D litecomp technology to evauluate production rate and product properties. 3D Litecomp is a sandwich technology developed at Chalmers Industrial Technology. The technology makes it possible to manufacture strong light stiff structures in complex shapes with high-energy absorption and variable sandwich core thickness.
2012 – 2013
The aim in this pre-study was to develop a methodology and predictive model to use as initial guidelines for minimizing the risk for hot cracks in MAG-welded T-joints. The model was verified against both specimens produced in the earlier project and against problematic applications from the industry.
2016 – 2017
This project will in a doctoral project develop models of how the cooling rate affects the fatigue strength so that production can quickly be adapted to new components and steel alloys in order to reduce lead times.
2016 – 2020
This prestudy aims at mapping the present situation in the Swedish composite industry, as well as adding the first pieces to a longterm strategy: For Sweden to establish a global position in the rational and efficient production of composites.
2017 – 2018
The HIPGEAR project introduces an innovative manufacturing technology for gear wheels intended for heavy vehicle applications.
2014 – 2018
The vision of the project has been to increase competitiveness in Swedish automotive manufacturing industry. The research objective of the project has been formulated as: to develop and test a generic methodology that facilitates systematic maintenance-related waste reduction in Swedish automotive manufacturing industry.
2013 – 2016
2013 – 2016
This project aims to enable robust spot welding of aluminum with existing infrastructure through innovative solutions.
2015 – 2016
The purpose is to investigate if two new types of sandwich materials, with cores of metal or wood, have the potential to meet requirements of mechanical properties,and manufacturing cost and time perspectives.
2012 – 2013
In the preliminary study, we intended to compile baseline information for future work in the scheduled main project
2012 – 2013
It is important for Swedish vehicle industry to continuously improve manufacturing processes to strengthen the compatibility and to keep production in Sweden.
2010 – 2011
The project's aim was to study how to create driving force for improvement work and development of production systems with increased environmental focus
2011 – 2013
The goal with the project is to develop technique for online-detection of weld defects in the automotive industry with laser induced ultrasonics. Methods for laser- and point welds will be developed.
2012 – 2013
Purpose and goal is to create industrial guidelines and recommendations concerning the forming of composite materials in traditional production processes.
2015 – 2018
2010 – 2014