Rikard Söderberg
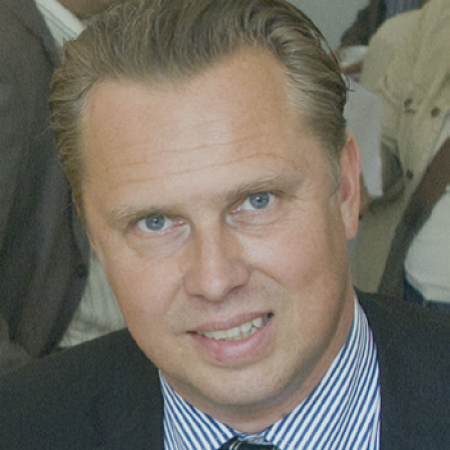
Project time: 2013 – 2015
Budget: 11 825 000 SEK
"Geometry Optimised adhesive joining for sustainable production” in Swedish (Geometri Optimerad LimFogning för hållbar produktion, "GOLF") is a project within the Swedish research program FFI for Sustainable production. It has as its mission to develop technology and methods to get the right amount of adhesive on the right place. The drivers behind this are the overall strive to decrease weight in vehicles and moving machines to minimize the amount of CO2 in the atmosphere.
The CO2 hunt, forces development of new material combinations in products that got to be more efficient. This material combinations causes some new joining situations where old knowledge of joining components of the same material are overruled by material combinations that can´t be welded or joined together with rigid joint methods that don´t take the different behavior of the joint material in account. Using adhesive as an joining method is not an new technology, but the use of adhesive in the way that the new material conditions put the demands on the parts and products is a new thing.
The car industry has used adhesive bonding for over thirty years. It has mainly been used as a sealing material in welded or riveted joints where the forces in the joints between the materials should have been carried out by the spot welds or rivets. The adhesives strength has been looked at as some kind of bonus in the total strength of the joint. This are shown in the facts around the data of stress analyses with FEM where there are very little traces’ of how to involve the strength of the adhesive in the structural analyses. Look at the thesis work (Effects of Cyclic Thermal Loadings on Distortion of Dissimilar Joined Materials) in the appendix A. There are almost no evidence of how to model the adhesion in the FEM solutions. Because of the history of joining technology the demands of which forces a joint should be able to wear there are no real design demands on the joint. The knowledge of how much stresses and in which directions it should work are based on the destructive testing that almost all car manufacturers uses to investigate that the joints are correct. One problem is that with the new materials and material combinations. The part price becomes much more expensive than with an all steel component. From around €5 to €20 per sheet metal part to €80 to €100 per multi material part, which means that destructive testing is not manageable any longer. This also means that process control to assure that the joining method delivers the joint that the designer intended is of most importance.
FFI Fordonsstrategisk Forskning och Innovation | www.vinnova.se/ffi 5
The process to create a more design directed requirements will take some time. In the mean while the knowledge around the process parameters to be controlled and monitored to be able to produce correct adhesive beads with placement control is of great importance.
The “GOLF” project had its start point from state of the art knowledge and technology of adhesive characterization, collision free path planning and advanced fluid simulation. The project aimed to through the rheology status of the adhesive create optimized robot programs to fulfill coming requirements of placement, amount and compensation. To meet the effects of assembly parts that have joining surfaces that are not geometrical optimal due to the theoretical ideal to mount the meeting surfaces parallel in normal direction. The deviations could come from parts that are deviating from the nominal form, it is not held in its nominal shape during assembly or the shapes of the parts can´t be assembled with all joints in normal direction. There will be sliding or tilting conditions during closing the gap between the parts. This has been studied in the project in a comparable small study to investigate which forces the parts puts on the bead and which forces the bead reacts with, that can change the shape and imply stresses in to the parts during fixation and curing. The study showed how complex the forces in the gap directs the effects on the adhesive and the parts which must be carried out in a continuation project.
The aim was to identify the potential of a new production method where components are produced by partial forging of ductile cast iron.
2013 – 2014
The project is expected to result in strengthening the Swedish automotive industry competitiveness and also to reduce the environmental impact from heavy duty vehicles.
2015 – 2016
The objective was to test strength, stiffness, production cycle time and cost for the rear end of a Volvo city bus using 3Dlitetechnology.The result is that the technology functions and that the the production cycle time is about 3 min for the core filling.The design has been compared with a carbon fiber structure and is as strong and stiff as the carbon fiber structure but to much lower cost.
2013 – 2014
2009 – 2012
The objective has been to manufacture components with low friction and high wear properties and reduce the need for post machining and straightening by utilizing the full potential of nitriding processes in combination with selection of steel grade
2009 – 2013
OptiDies has created new, in-depth understanding of the prevailing complex tribo-systems when forming AHSS. Skills involved are tribology, sheet and tool steel, die manufacturing methods, numerical analysis and cost modelling.
2009 – 2012
The HIPGEAR project introduces an innovative manufacturing technology for gear wheels intended for heavy vehicle applications.
2014 – 2018
The project goal was to create methods and tools for proactive assembly ergonomic and geometric quality assurance for sustainable production.
2013 – 2016
The project goal is to test manufacturing of a 7 m bus side using 3D litecomp technology to evauluate production rate and product properties. 3D Litecomp is a sandwich technology developed at Chalmers Industrial Technology. The technology makes it possible to manufacture strong light stiff structures in complex shapes with high-energy absorption and variable sandwich core thickness.
2012 – 2013
An effective process can be realized only if there is a mechanism that facilitates information exchange and reuse of models and knowledge.
2009 – 2013
The aim with the project is to test a new method to join thermoplastic composite to metal in a lap joint by using a focused TIG arc, as a heat source, to heat the metal side just enough so that the composite melts and join to the metal. The method gives single sided access, no need for additional filler material and makes invisible joints possible. The objective is to have a joining method that is robust, gives high productivity and high quality as well as cost advantages.
2012 – 2013
2010 – 2011
The project has studied how the silanoles are affected by different treatments.
2013 – 2016
The study includes a literature study, the test of different electrochemical solutions, and the design of a simplified setup for performing LECD. At the end of the feasibility study, sufficient knowledge should be achieved to evaluate if LECD can be a potential method for localized treatment in the context of re-manufacturing.
2015 – 2016
2013 – 2015
This project was using electromagnetic pulse power to develop a new unique innovative production process in the following area: Adiabatic cutting/shearing – The major benefit is the ability to create holes in steel sheet materials by single side punching holes.
2010 – 2012
In the preliminary study, we intended to compile baseline information for future work in the scheduled main project
2012 – 2013
The project aims to develop a new type of abhesion multilayer system based on the combination of layers with different mechanical/physical properties that can provide customized features for wear, friction, adhesion and wettability
2012 – 2013
The paintshop is often a bottleneck in production and the processes are fine-tuned based on testing on numerous prototypes. To meet the future demands there is a great need to improve the product preparation process. The aim is to develop methods, techniques and software, and supporting measurement methodology, for simulation of paint curing in IR and convective ovens. The goal is to assist the industry to further develop and optimize their surface treatment to be more energy and cost efficient; to have a shorter lead time in product development; and to give a higher product quality.
2016 – 2019
The goal of this project is faster product realizations of hybrids and fully electrified light weight vehicles by developing digital tools for efficient geometrical packing and assembly path planning and analysis of flexible parts.
2009 – 2013
2009 – 2011
Protecting key competence in a global business environment requires control of intellectual properties (IP). The project will test how to specify the manufacturing of a product (Know how) without revealing the product IP (Know why).
2012 – 2013
2014 – 2015
This prestudy aims at mapping the present situation in the Swedish composite industry, as well as adding the first pieces to a longterm strategy: For Sweden to establish a global position in the rational and efficient production of composites.
2017 – 2018
Finding effective ways for skills and technology diffusion (K & TS ) of research and coordination of educational resources is a strategic area for Swedish industry to master. The need for training at all levels to cope with future products , materials and processes will increase.
2013 – 2014
The basic idea behind the project Additive Manufacturing of metal cutting tools was to utilise so called additive manufacturing technology to produce metal cutting tools used by the automotive industry to manufacture power transmission gears.
2013 – 2016
The project aims to increase the knowledge about the mechanisms controlling the polishability of coated surfaces to facilitate the development and implementation phase of new and more environmental friendly coating systems.
2016 – 2019
This project focuses on the development of a new generation of fasteners B14 with a significantly higher strength than the conventional fasteners 10.9 and 12.9 used today, i.e. the new fasteners have a target tensile strength higher than 1400 MPa combined meantime with satisfactory ductility
2011 – 2013
This project is aimed at developing competitive light weight steel solutions for the car body by reducing the density of the blank material without any major change in the elastic stiffness. The low density steel blank is a laminate (sandwich) with outer layers of ultra-high strength steel and low density core created by sintered metal powder.
2013 – 2016
The project results show that it is possible to accurately simulate spray painting of a truck cab or a car in only a few hours on a standard computer.
2009 – 2012
The project will develop a non-destructive testing method based on laser-ultrasonics (LUS) aiming for mechanized quality control of joints in industrial environments.
2014 – 2017
Operation planning systems based on standardised international and generic models for communication and interaction and which easily can be adapted to company needs will give great advantages.
2009 – 2013
This project will in a doctoral project develop models of how the cooling rate affects the fatigue strength so that production can quickly be adapted to new components and steel alloys in order to reduce lead times.
2016 – 2020
By combining sheet metal forming technology with CRTM processes and highly reactive matrix material the goal are to reach same production rate as for sheet components
2012 – 2013
Robust laser welding of aluminium by using innovative laser welding tools and prediction models to avoid cracking and distortions
2017 – 2020
2014 – 2015
The project objectives were to understand if atmospheric plasma could act as cleaning and activation process before bonding and allow for an implementation with a moderate investment cost of a process that is generic for a variety of applications.
2012 – 2013
The overall purpose of this project has been to demonstrate how a model-driven workflow can streamline process planning and quality assurance. Model-driven process planning and quality assurance has great potential to contribute to a significant productivity increase in process planning and quality assurance.
2014 – 2017
Increase competitiveness by developing complete work chain from virtual preparation, through automatically generated PLC code, to virtual and physical commissioning.
2014 – 2017
The combination of ultra high strength steels and aluminium is expected to play a large role in the vehicles of the future. In the project we test the hypothesis that friction stir welding can be used to create high performance joints.
2012 – 2013
The press hardening process is based on the forming of hot blanks, in the austenitic state, to improve the formability as well as obtaining a final martensitic structure by subsequent rapid cooling in the forming tools
2010 – 2012
2009 – 2013
The project is aimed at developing and testing a new principle for dynamic planning and preparation of assembly where balancing is optimized at a higher system level, considering assembly sections rather than stations, which is common today. This would entail significant savings since today’s view of the workstation concept creates a discrete, inflexible entity with balancing losses
2012 – 2013
To improve accuracy and usability for simulation of compression moulding through two PhD-students focusing on long and short fibre composites.
2017 – 2019
The project's main goal is to develop a design and manufacturing methodology, for resource efficient additive manufacturing of components in the automotive industry.
2017 – 2020
The purpose of this project is to adopt and to demonstrate a system for automatic inspection of all manufactured components in-line in a production line.
2017 – 2020
The aim in this pre-study was to develop a methodology and predictive model to use as initial guidelines for minimizing the risk for hot cracks in MAG-welded T-joints. The model was verified against both specimens produced in the earlier project and against problematic applications from the industry.
2016 – 2017
2010 – 2014
To replace the manual inspection, minimize the consequences of defects and to improve the quality of delivered products with an efficient and automated Quality Control system.
2016 – 2019
This project enables more extensive utilization of virtual tools based on increased access to the manufacturing related data.
2009 – 2012
2011 – 2013
2014 – 2017
Develop innovative concepts for in-line NDT of heat treated components, hence minimizing the need for costly and time consuming destructive testing.
2015 – 2018
SIMET GICP has been a very successful research project and has resulted in a task model for the systematic measurement technology planning and preparation.
2009 – 2013
2012 – 2015
The aim of the project was to create 10 new modules for continuous education and training for professionals and students in undergraduate education.
2014 – 2016
The project focuses on how to reduce waste/cost caused by environmental aspects and adding value to the production system by green strategies and actions
2009 – 2012
With globalization and other megatrends as demographic changes and climate change, more knowledge is needed regarding production in an international perspective. PADOK Study Visit in India 2016 have given an increased knowledge regarding how production is conducted in India, some of the challenges producing companies in that region is facing and how Swedish companies interested in investing in production in India could act to establish themselves in the region.
2016 – 2016
2017 – 2018
The aim is to facilitate an increase in use of nitriding processes in order to create surfaces with high strength and friction and wear properties
2014 – 2017
The overall objective of the project was to: • Develop simulation methodology for drive simulation of transmissions with given shape, surface topography and surface structure, - for more robust and better prediction of the efficiency and life of gear contacts in gearboxes. • Through experimental evaluation and characterization, support and verify the developed simulation technology • Through experimental evaluation and characterization, further verifying the potential of using the correct surface texture, e.g. honing, and right-handed gear in heavy-duty transmissions.
2016 – 2018
The project has addressed challenges in casting and realisation of new cast irons with improved properties and machinability, decision making regarding manufacturing strategies and machinability of materials. Silicon-alloyed compacted graphite iron (CGI) has been demonstrated av new alternative for future engine components. New simulation technique for assessing manufacturing strategies has been introduced. Generic know ledge has been developed w hen it concerns w ork material machinability w ith specific reference to combined materials in advanced components.
2012 – 2015
The project QScrew aims to create improved processes for the design, testing, validation and assembly of bolted joints.
2015 – 2017
2009 – 2013
The objective with this project is to develop a new innovative process technology for the press hardening process.
2009 – 2011
In this project, a pre-treatment of uncoated boron steel has been investigated, which after hot stamping results in the formation of an oxide showing excellent adhesion to the steel
2012 – 2014
The project “Design of Materials Preparation Processes” deals with materials preparation as a means for the production system to manage the increasing numbers of component variants, which is an ever growing challenge in modern assembly operations.
2014 – 2017
The surface treatment is the process in an automotive factory that consumes most energy, water and chemicals, and produces most waste and pollution
2012 – 2015
The hypothesis is that assembly of future light-weighted vehicles drastically will change the vehicle production process. The aim is to identify future production process and future research areas.
2012 – 2013
2010 – 2011
2009 – 2013
The project LISA2 will deliver industrial-ready services enabling Swedish industry to understand and tune their factories
2015 – 2018
Syftet var resultatsspridning och detta uppfylldes verkligen med 104 högkvalitativa presentationer för industri
2011 – 2012
There is an urgent need for Swedish industry to explore strategies and methods to accelerate the efficiency progress and support decision making in order to regain profitability.
2009 – 2012
Predictive process models for thermo-mechanical forming processes like press hardening have been developed during this project
2011 – 2014
The project is mainly addressed to manufacturing of components and sustainable production engineering
2011 – 2012
Our hypothesis is that advanced, lightweight, multi-layer-structured composites with good barrier properties and tailored biodegradability can be produced by combining bio-based thermoplastic with special additives and pulp fiber mats. This material is free from fossil raw materials, sustainable, fire and impact-resistant and suitable for interior components in vehicles.
2012 – 2013
The project’s objective has been to produce instructions, calculation models and other tools to facilitate optimized construction and production of screw joints.
2009 – 2011
2013 – 2014
The vision of the project has been to increase competitiveness in Swedish automotive manufacturing industry. The research objective of the project has been formulated as: to develop and test a generic methodology that facilitates systematic maintenance-related waste reduction in Swedish automotive manufacturing industry.
2013 – 2016
2011 – 2014
2009 – 2011
In this project, we focus on two methods to make gears more high-strength, namely to replace gear milling with gear rolling based on plastic forming and the introduction of clean steels with reduced inclusion content
2012 – 2015
The purpose is to investigate if two new types of sandwich materials, with cores of metal or wood, have the potential to meet requirements of mechanical properties,and manufacturing cost and time perspectives.
2012 – 2013
Validate previously developed failure models on component level. Implement models into a commercial code. Shorten lead time for new advanced components. 15 % weight reduction.
2015 – 2018
Flexible assembly for Considerable Environmental improvements of CAR's
2009 – 2012
This project aims to assess easier and cheaper quality assurance of spotwelded joints by controlling the electrode indentation.
2016 – 2017
2010 – 2012
The purpose of this project is to bridge the gap betweenmechanical and electrical engineers in order to achieve a more efficient productionpreparation, enabling virtual commissioning and automatic generation of verified controlprograms.
2009 – 2012
To develop methods and models for prediction of die conditions in press hardening
2014 – 2017
The overall goal was to gain experience from a full-scale demonstrator in Saab´s paintshop with emphasis on energy saving in Swedish automotive paintshops. Paintshops are the largest consumers of energy in these factories
2011 – 2012
A study “before and after” EnviroMan, indicates that the project has created increased understanding on specific topics and also useful results
2012 – 2015
Gear transmission products are strategically important key components in powertrains produced by the Swedish automotive industry
2009 – 2012
In this projectthree areas of component realization are covered: casting, heat treatment and machining.
2009 – 2012
In material handling processes, such as kitting and sequencing, which are used in the automotive industry to supply the assembly with a wide and growing range of component variants, the picking information system is central design aspect. Given the developments in digitization, the purpose of this concept study is to evaluate the potential of digital technology to support materials handling work in production systems.
2017 – 2017
2013 – 2016
All manufacturing processes are afflicted by variation which may violate the fulfilment of assembly requirements, functional requirements or esthetical requirements. Another issue is the difficulties to reach desired form in all areas.
2009 – 2013
The aim of the project is to investigate the synergies obtain by a holistic optimization framework that simultaneously optimize the product, the production system, and the manufacturing processes.
2012 – 2013
The proposed project aimed to implement the digital human modelling tool IMMA in Swedish industry and universities.
2013 – 2016
This research project has studied the influence on the accuracy of FE-predictions of springback in sheet metal forming from different material models
2010 – 2012
The project ALKOMP have addressed challenges with aluminum in sheet forming
2012 – 2015
2012 – 2015
2014 – 2014
The project is based on the hypothesis that it is possible to establish measurable objective evaluation criteria of characteristics for joining in various combinations of materials.
2012 – 2013
Future sustainable competitive production systems need to be productive and flexible, as well as environmentally friendly and safe for the personnel
2011 – 2014
The integration of data management systems, simulation software and optimization algorithms have been shown to increase throughput in existing production but also allow expanded use of virtual tools in the preparation phases. This in turn leads to shorter development times for new production systems and products. The project has also contributed to greater understanding and concrete improvements in the processes of collecting and assure the quality of production data. This in turn increases the quality in both simulations and direct data-driven analyzes.
2013 – 2017
This project will address some of the main obstacles in introducing FSW as a flexible joining process within vehicle production.
2009 – 2012
The Hotform Project set out to obtain robust physical data on the hot forming process for use in improving the quality of finite element simulations used in the design and verification of parts and tooling for manufacturing press hardened auto body components
2012 – 2014
2009 – 2012
We have built a Swedish Research Park for development and test of calibration processes for alcolock prototypes, aiming at a future high-volume production
2012 – 2014
Further development of solutions for powerful collaborative robots, focusing on safety issues and the use of an enabling device.
2015 – 2018
The project's aim was to study how to create driving force for improvement work and development of production systems with increased environmental focus
2011 – 2013
2012 – 2013
The projects aim was to combine the technologies from virtualization to digitalize the methods from visualization in order to enable their usage in global teams as well as to create transparency between knowledge work and the management of the knowledge needed for the execution and improvement of that knowledge work
2012 – 2015
2014 – 2017
Purpose and goal is to create industrial guidelines and recommendations concerning the forming of composite materials in traditional production processes.
2015 – 2018
The project intends to translate the new information into improved procedures and processes in the automotive industry
2012 – 2014
This project is part 2 of the PhD project "Modelling and simulation of simultaneous forming and quenching of Boron steel" funded by VINNOVA.
2008 – 2012
The aim of the project has been to create a stable, reliable and verified concept for hemming of lightweight structures in multi-material, including virtual tools to determine sealed joints. This also ensures the quality costs since corrosion will not occur and thus facilitated the introduction of new lightweight materials.
2014 – 2017
This hypothesis will investigate the potential of tooling solutions and other methods, considering demands from technology, business models and communication.
2012 – 2013
2013 – 2017
This project addresses challenges of sustainable manufacturing of high-added value powertrain components involving efficient and robust machining of advanced materials.
2009 – 2012
The goal with the project is to develop technique for online-detection of weld defects in the automotive industry with laser induced ultrasonics. Methods for laser- and point welds will be developed.
2012 – 2013
The following project aim to develop test routines for coating systems, in order to secure final surface quality when new coating systems are introduced in production
2013 – 2014
The hypothesis has been inspired by materials that consists of fibers can be more easily cut with a blade using wavy profile. The cutting motion is important, is it possible with the help of ultrasound to create a more favorable cutting motion.
2012 – 2013
The project will develop design solutions where existing/modified joining techniques are used for joining of new lightweight materials to more traditional materials
2016 – 2019
This project aims to enable robust spot welding of aluminum with existing infrastructure through innovative solutions.
2015 – 2016
The goal of the project was to implement a new quality system for welding in design and manufacturing of welded components
2010 – 2012
2013 – 2015
The manufacturing time of sintered steel components will be reduced by using induction sintering. The following surface hardening with induction aims at increasing the performance and therewith the possible applications.
2012 – 2013
This research project (ONWELD) serves to investigate and verify the potential for new laser scanning technologies and developed algorithms as a modern tool for automated, unbiased geometrical weld quality assurance.
2013 – 2016
The project has confirmed the hypothesis that tailoring of the tempering is a functioning means of making PM steel sustainable towards high static loading in potential automotive applications. The project has also developed further understanding about mechanisms that could be responsible for static loading sensitivity with respect to creep/relaxation at slightly elevated temperature. The results relate to sustainable manufacturing processes, the basis being that powder compaction and sintering is an energy efficient way with high raw materials utilization.
2012 – 2013
Develop manufacturing technologies where composites are integrated directly to metals in production systems for press hardened boron steel and hot-formed aluminum.
2015 – 2016
The project goal is to minimize distortion of hardened components by evaluation and minimising effects from factors causing distortion potential in the process chain.
2015 – 2018
The objective is to evaluate the suitability of additive technology for creating possibilities for the use of new materials and new processing strategies in the production of lightweight components with high demands on product characteristics and reasonable production costs.
2012 – 2013
The aim of Lightstruct is to develop conditions to manufacture lightweight welded structures within construction machineries
2012 – 2014
Increased demands on an efficient and sustainable automotive industry, driven by international competition and global demands on reduced use of resources, requires more efficient manufacturing systems
2011 – 2013
It is important for Swedish vehicle industry to continuously improve manufacturing processes to strengthen the compatibility and to keep production in Sweden.
2010 – 2011
The project aimed to develop a concept for self-piercing riveting in material combinations that are not recommended to join together with self-piercing riveting. This is by using the so called “Plugg-concept”.
2013 – 2016
2013 – 2016
It is a key issue for the automotive manufacturing industry to sense, and to have the ability to act on changes on the market with respect to environmentally friendly and lightweight products
2011 – 2014
2009 – 2012
The main aim with the project was to create solutions that enable globalization of production by using smart ICT-tools.
2013 – 2015
2011 – 2013