Magnus Lundgren
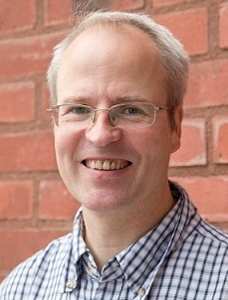
Projekttid: 2009 – 2013
Budget: 21 350 000 kronor
Projektets utgångspunkt var att verka för och främjautveckling av effektiv datorstödd produktionsberedning.
Detta projekt har syftat till att ta fram ny kunskap och utveckla teknik som möjliggör försvensk fordonsindustri att på ett konkurrenskraftigt sätt bedriva kunskapsbaseradproduktion i Sverige och därigenom medverka till en fortsatt konkurrenskraftigfordonsproduktion i Sverige. Produktionsberedning är enmycket central process i ett tillverkande företag och syftet med denna är att utvecklabästa möjliga tillverkningslösning. Omfattningen av produktionsberedning kan därförvara stor, alltifrån konceptuell beredning till detaljerad operationsberedning. Dettaprojekt har fokuserat på modelldriven formelementbaserad operationsberedning. Medmodelldriven menas ett arbetssätt i vilket man använder digitalt representerade modellerav produkter, råämnen, fixturer, verktyg, maskiner m.m. som tillhandahåller informationom material, formelement, tillverkningskrav och toleranser m.m. En grundtanke i detmodelldrivna arbetssättet är att produkten kan beskrivas som bestående av olikaformelement (plan, hål, spår m.m.) för vilka det finns olika metoder att framställa demmed. Vilken metod som är mest lämpad avgörs dels av de tillverkningskrav ochtoleranser som finns angivna, men också utifrån beredarens erfarenhet och vilken praxissom råder på det tillverkande företaget. Ett grundläggande syfte med det modelldrivnaarbetssättet är att med datorteknik och programvara för framtagning, visualisering ochinteraktion med modeller stödja mänskligt kunnande och expertis. Under projektet harforskargruppen i samarbete med industripartners och systemleverantörer undersökttillämpbarheten av modelldriven operationsberedning genom kartläggning av industrinsbehov, studier av tillgänglig programvara för operationsberedning, samt studier avinternationella standarder för informationsmodellering för produkt-, process- ochresursrepresentation. Industrins behov har kartlagts genom workshops, studiebesök ochgemensamma arbetsmöten. Systemleverantörspartnerna i projektet har i olika workshopssamt i mindre enskilda projekt tillsammans med de deltagande tillverkningsföretagendemonstrerat vad deras beredningssystem är kapabla till. Utifrån detta harforskningsutförarna formulerat idéer och förslag på aktiviteter att genomföra sompresenterats och diskuterats vid regelbundna gemensamma arbetsmöten. Baserat pååterkoppling från industrideltagarna har dessa förslag och idéer sedan vidareutvecklats tillflera olika prototypapplikationer för demonstration av modelldriven operationsberedning. Projektet har också samarbetat med FFI-projekten Digital Factory och Robust Machining,samt deltagit i internationellt samarbete gällande informationsmodellering. Ett samarbetedär projektet har levererat viktiga bidrag inom området kinematikrepresentation. Resultaten från detta projekt är i ett långsiktigt perspektiv viktiga bidrag för att ökaproduktiviteten och kvaliteten inom operationsberdedning och i tillverkningsprocessen. Det nära samarbetet mellan forskningsutförarna och industrideltagarna i projektet harbidragit till att bibehålla och i viss mån också förstärka de sedan många år godarelationerna mellan svensk produktionsforskning och svensk fordonsindustri. Genomolika demonstrationer, har projektet inte bara kommunicerat möjliga fördelar med ettmodelldriven operationsberedning till industrin. Projektet har dessutom visat att det ärmöjligt att genomföra den demonstrerade funktionaliteten baserat på systemneutralainternationella standarer för informationsmodellering. De flesta av projektetsdemonstrationer har också uppmärksammats internationellt och erkänts som viktigabidrag inom Virtual Manufacturing. Svensk produktionsforskning inom informationsmodelleringför industriell tillämpning har internationell sett en framstående position. Föratt bibehålla denna position är det därför viktigt att fortsätta med forskning inommodelldriven beredning, där ett lämpligt område att fortsätta denna forskning är Production Part Approval Process (PPAP). PPAP används inom fordonsindustrin för attskapa förtroende för komponentleverantörer och deras tillverkningsprocesser och syftetmed PPAP är att säkerställa att en leverantör har förstått alla produkt- ochtillverkningskrav för de komponenter de levererar, och att leverantörens tillverkningsprocessär kapapel att tillverka produkter enligt angivna produkt- och tillverkningskrav. Nuvarande PPAP är dock en arbetsintensiv process där produktionsberedare måste ägnavärdefull tid på det icke värdeskapande arbetet med att ta fram alla de nödvändigadokument PPAP kräver. Att ersätta dagens arbetskrävande och dokumentbaserade PPAPmed en modellbaserad dito skulle effektivisera nuvarande PPAP och öka produktiviteteninom såväl produktionsberedning samt i produktionen.
Projektet syftade till att sänka kostnaden för synliga exteriöra fogar på fordon genom att använda båglödprocesser
2011 – 2013
Syftet var att provtillverka en stor komplex barande fordonsstuktur for att utvardera hur snabbt man kan till lagt pris kan tillverka denna med 3DLiteteknologi. Vi har valt Volvo Buss bakstam till city bussar. Samliga mål uppnåddes i projektet men tillverkning av bakstammen pga design (stylingandring) pa bussen forskjuts till senare delen av hosten 2014
2013 – 2014
Omställningen från konventionella till elektriska drivlinor skapar många utmaningar, men öppnar även för nya möjligheter rörande komponentpackning och utformning av bärande strukturer samt nya tillverkningsmetoder för dessa. Projektet syftar till att nyttja möjligheter med sandwichkonstruktion för att sänka vikten och därmed energiförbrukningen för framdrift; minska värmeförluster och därmed energiåtgången för klimathållning; minska tillverkningskostnader med hjälp av nya tillverkningskoncept, rationell sammansättning och ny konstruktionsteknik.
2017 – 2020
Målet var att studera hur drivkraft för förbättringsarbete och utveckling av produktionssystem med ökat miljöfokus kan skapas
2011 – 2013
2012 – 2014
Projektet ska utveckla en oförstörande mätmetod baserad på laserultraljud (LUS) i syfte att möjliggöra automatiserad kvalitetssäkring av fogar i industriella miljöer.
2014 – 2017
Det övergripande syftet med SUSTAIN-CRYO-projektet är att utveckla kylnings/smörjningsmetoder som möjliggör miljö-neutral produktion i Sverige.
2017 – 2020
Detta projekt kommer att inrikta sig på några av de största hindren för införandet av FSW som en flexibel process inom fordonsproduktion. En stor del av projektet innebär att utveckla kunskap om möjligheter och begränsningar vid användandet av robotiserad FSW
2009 – 2012
Validering av tidigare utvecklade brottmodeller på komponentnivå. Implementering av modeller i kommersiell kod. Kortare ledtid för avancerade komponenter. 15 % viktminskning.
2015 – 2018
2010 – 2012
2013 – 2016
2013 – 2016
2012 – 2015
2011 – 2013
2013 – 2014
Med den globalisering som skett inom marknaden för tillverkade produkter, kombinerat med megatrender som klimatförändringar och demografiska förändringar, behövs mer kunskap kring hur produktion ser ut i andra regioner. PADOK Study Visit in India 2016 har gett en ökad kunskap inom hur produktion genomförs i Indien, vilka utmaningar tillverkande industri där ställs inför och hur svenska företag intresserade av att investera i produktionsanläggningar i Indien kan agera för att enklare etablera sig.
2016 – 2016
Projektets övergripande mål har varit att skapa ett stabilt, tillförlitligt och verifierat koncept för falsningsprocessen av lättviktsstrukturer i multimaterial samt virtuella verktyg för att prediktera ett förbands täthet. Såväl limparametrars som falsparametrars inverkan har studerats och analyserats i syfte att även förbereda för kombinationer av material där täthet och galvanisk separation blir kritiskt
2014 – 2017
Resultatet kommer att utvärderas enligt teknisk prestanda och företagen kommer att utvärdera processen i demonstratorer, förberedande industrialiserings studie och hållbarhetsbedömning.
2017 – 2019
Projektets syfte är att minska ledtiden för pressverktyg genom ökad leverantörssamverkan och forskning.
2017 – 2020
Målet är förbättrad hållfasthet med mer än 15% (tre gånger längre livslängd) genom styrd kylning vid sätthärdning för drivlinekomponenter.
2016 – 2020
På det stora hela har projektet kunnat uppfylla sitt övergripande syfte som var att bygga tillräckligt med kunskap om de visuella metoderna för att digitalisera dem på ett sätt som möjliggör deras användning i globala team samt för kontinuerlig förbättring utan att negativt påverka metodernas enkelhet och användbarhet
2012 – 2015
Syftet är att testa ett nytt sätt att foga termoplastisk komposit mot metall genom att i en överlappsfog värma den fria metallsidan, med en extra fokuserad TIG ljusbåge som värmekälla, till dess att kompositen precis smälter så att vidhäftning erhålls mot metallen. Metoden ger fördelar som enkelsidighet, inget behov av extra tillsatsmaterial och möjliggör osynliga fogar. Målet är att få en fogningsmetod som är robust, ger hög produktivitet och hög kvalitet samt kostnadsfördelar.
2012 – 2013
Projektet syftar till att långsiktigt stärka forskningsmiljöer och forskningsområden inom produktionsteknik för att lösa problem som aktualiseras av ökande miljökrav och krav på krockprestanda.
2009 – 2013
Projektet adresserar utmaningar avseende uthållig produktion när det gäller högt förädlade drivlineprodukter där robust bearbetning av anvancerade material är centralt.
2009 – 2012
2014 – 2017
Projektets mål är att utveckla nya simuleringsbaserade metoder för optimering och kunskapsalstring. Dessa metoder ska kunna användas som stöd när företag ska fatta lönsam och hållbar beslut om sin produktion.
2009 – 2012
Detta projekt syftar till att möjliggöra robust punktsvetsning av aluminium med befintlig infrastruktur genom innovativa lösningar.
2015 – 2016
Denna förstudie ska föreslå sätt att förbättra konventionella båglödningsmetoder så att de kan ersätta laserlödning. Om samma fogtyp och kvalitet kan uppnås som med laserlödning, så åstadkoms en avsevärd kostnadsreduktion jämfört med de i dag förekommande alternativen.
2010 – 2011
Målet är att ta fram en riktningsprocess med minimal inverkan.
2009 – 2011
2012 – 2015
Projektet fokuserar på montering av optimerade skruvförband för lättviktskonstruktioner.
2009 – 2011
2016 – 2016
Ett fordonsmåleri är den i särklass största energislukaren i dagens bilfabriker, och målet var att sprida kunskap bland svenska fordonsmålerier.
2011 – 2012
Projektet har tagit fram ett antal konceptuella metoder och ger förslag på ett samlat paket med insatser som radikalt kommer att öka verkningsgraden då det gäller tekniköverföringen från forskningsprojekt inom FFI programmet och generellt.
2013 – 2014
2010 – 2012
Flexible Assembly for Considerable Environmental improvements of CAR's
2009 – 2012
Projektet DAIMP syftar till att öka produktivitet, robusthet och resurseffektivitet i produktionssystem genom datadriven underhållsplanering. Projektmålen är: överenskomna dataparametrar och alarmstrukturer för analyser och mätetal ökad dataanalys för underhåll genom prediktiv och normativ analys ökad användning av dynamisk datadriven kritikalitetsanalys ökad prioritering av underhållsaktiviteter
2016 – 2019
Målet med projektet är att demonstrera detta koncept i en fullskalig produktionslina och genom utvärderade prototyper inom en eller två av följande produktgrupper: säten, tak, stolpar, solvisir och bagageutrymmen.
2017 – 2020
2009 – 2013
ReLed-3D Resurseffektiv och flexibel produktion inom fordonsindustrin genom additiv tillverkning i metall
2017 – 2020
Sammanställningen av studierna förväntas leda till en samsyn kring polerbarhet och en föreslagen metod för hur framkomna resultat ska kunna kommuniceras och omsättas i praktiken.
2016 – 2019
Förstudiens mål att sammanfatta projektdeltagarnas interna kunskap samt kartlägga den externa kunskap som finns inom området polering av klarlack/solidlack har uppfyllts. Detta har gjorts genom kunskapsutbyte, omfattande litteraturstudie och workshop med deltagande av externa aktörer.
2013 – 2014
2012 – 2014
Huvudmålet att korta ledtid och kostnad för framtagning av nya aluminiumkomponenter uppnås om t ex färre iterationer för utprovning av nya verktyg till nya detaljer behövs
2012 – 2015
Öka konkurrenskraften genom att utveckla hela arbetskedjan från virtuell beredning, via automatiskt genererad PLC-kod, till virtuell och fysisk idrifttagning.
2014 – 2017
Den Virtuella Målerifabriken - Simulering av Ugnshärdning. Måleriet är ofta en flaskhals i produktion där processerna idag finjusteras genom testning på ett stort antal prototyper. För att kunna möta framtidens behov så behöver produktionsberedningen kraftigt förbättras. Syftet är att utveckla metoder, tekniker, mätmetodologi och mjukvara, för simulering av härdning av färg i IR och konvektionsugnar. Målet är att stödja industrins utveckling och optimering av ytbehandlingsprocesserna så att dessa blir mer energieffektiva; har en kortare ledtid i produktutvecklingen och ger bättre kvalitet.
2016 – 2019
Etablera en förstärkt kunskapsplattform kring tillgängliga additiva tillverkningstekniker för att skapa förutsättningar för användning av nya material och nya beredningsstrategier för framtagning av lättviktskomponenter.
2012 – 2013
Projektets mål var att utveckla ett koncept för en fogningsmetod för icke formbara material i kommande multimaterialprodukter
2013 – 2016
2013 – 2015
Detta projekt avser att möjliggöra enklare och billigare kvalitétssäkring av punktsvetsade förband genom kontroll av elektrod-indentering.
2016 – 2017
Projektet har inriktats mot att ta fram robusta fysiska data med vars hjälp varmformningsprocessen kan beskrivas och kvaliten på FE simulationer förbättras
2012 – 2014
Att öka noggrannheten och användbarheten vid simulering av formpressning genom två industridoktorander som fokuserar på kort- respektive långfibriga kompositer.
2017 – 2019
Projektet kommer ta fram konstruktionslösningar där befintliga/modifierade fogningsmetoder används för fogning av nya lättviktsmaterial till mer traditionella material
2016 – 2019
2013 – 2016
Projektet QSkruv har som mål att skapa förbättrade processer för konstruktion, utprovning, verifiering och montering av skruvförband.
2015 – 2017
Projektets syfte är att utveckla teknik som ta sikte på de övergripande målen om en högre produktivitet samt en minskad miljöpåverkan och bidrag till reducerad CO2 användning genom repeterbara och kvalitetssäkrade limfogar för framtida multimaterialanvändning
2016 – 2019
Målet är att inom 5 år etablera en tillförlitlig process som kan ersätta dagens ED-lackering och zinkfosfatering för fordonstillverkarna och deras underleverantörer.
2009 – 2012
2013 – 2015
Inom bilindustrin är designen av kaross-sammansättningsstationer fortfarande i hög graderfarenhetsbaserad. Vidare visade MERA projektet på kopplingar mellan geometrisk kvalitetoch resursutnyttjande. Därför behandlas i detta projektet konstruktionsparametrarna hos enkarossmonteringsstation tillsammans, med avseende på resursutnyttjande samt geometriskkvalitet.
2009 – 2012
2011 – 2014
Hypotesen har inspirerats av att material som består av fibrer lättare kan skäras med en egg bestående av en vågig profil. Den skärande rörelsen är också av vikt, går det med hjälp av ultraljud går att skapa en merfördelaktig skärrörelse.
2012 – 2013
2012 – 2015
I materialhanteringsprocesser, såsom kitting och sekvensläggning, vilka används inom fordonsindutrin för att försörja monteringen med ett stort och ökande sortiment av komponentvarianter, är det arbetsplatsnära informationsystemet en central aspekt i utformningen. Givet utvecklingen vad gäller digitalisering, syftar denna konceptprövningsstudie till att utvärdera potentialen för digital teknik att stödja materialhanteringsarbetet inom produktion.
2017 – 2018
2011 – 2012
2010 – 2012
För att svensk industri ska undvika att förlora intellektuellt kapital vid globala affärer, är projektets mål att testa hur man kan specificera hur en produkt ska tillverkas (´Know how´) utan att produktens IP (´Know why´) avslöjas.
2012 – 2013
Projektets mål är att upprätta mätbara objektiva utvärderingskriterier av fogegenskaper för kombinationsförband i olika material.
2012 – 2013
Målet med projektet är att skapa en komplett multifysikplattform för simulering av termo-mekanisk formning som tar hänsyn till verktygsslitage
2011 – 2014
Målet med projektet är att tillverka komponenter med mycket goda friktions- och nötningsegenskaper för minskad bränsleförbrukning samt att minska behovet av efterbearbetning och riktning genom att utnyttja fördelarna med nitrerprocesser ikombination med val av stål
2009 – 2013
För att besvara projektets forskningsfrågor och uppnå angivna målsättningar har följande metoder tillämpats. - Litteraturstudier - Studier av datorstöd för artikelberedning- och kvalitetssäkring - Workshopar - Fallstudier
2014 – 2017
Projektet kommer att genom experiment analysera en snabb tillverkningsprocess av kolfiberkomponenter med samma teknik som för plåtformningsprocesser och målet är att nå samma produktionstakt.
2012 – 2013
Ersätta manuell inspektion, minimera reparationskostnader och förbättra kvaliteten på produkterna, med ett effektivt och automatiserat Kvalitetskontrollsystem.
2016 – 2019
Projektet har handlat om att erbjuda och genomföra kursupplägget ´Från beslutsmeddelande till slutrapport´ för projektledare av, under 2016 nystartade FFI-projekt. Kursupplägget har erbjudits till totalt 66 projektledare vid två olika tillfällen. 14 projektledare har tackat ja och deltagit och dessutom tre deltagare från FFI-programledning.
2016 – 2016
Projektet syftar till att utvärdera om två nya typer av sandwichmaterial, i metall respektive trä, uppfyller dagens krav på mekaniska egenskaper, tillverkningskostnader och produktionshastigheter.
2012 – 2013
SIMET GICP har varit ett mycket framgångsrikt forskningsprojekt och har utmynnat i enaktivitetsmodell för systematisk mätteknisk planering och beredning.
2009 – 2013
Projektet genomförs i delprojekt i samarbete mellan Gestamp och SKF. Akademi och externt institut engageras för några av forskningsfrågorna. Prototypdetaljer kommer att tillverkas som verifieras enligt gällande krav
2010 – 2012
Hypotesen syftar till att utvärdera metoder att öka materialutnyttjandet vid plåtformning. I analysen ingår teknisk och miljömässig bedömning av potentialen för ökat materialutnyttjande, samt en utredning av de affärsmässiga och organisatoriska förändringar som krävs för att implementera metoderna
2012 – 2013
Syftet med projektet vara att utveckla och utvärdera en FE-modell för bedömning av varmsprickrisken i MAG-svetsade T-förband. Målet anses vara uppnått då resultaten från simuleringarna visar att det är möjligt att använda den utvärderade modellen för att bedöma sprickrisken i olika förband och jämföra olika fogprepareringar.
2016 – 2017
Inom projektet har det utvärderats om det är möjligt att erhålla en självsmörjande yta av inorganiska fullerener på verktygsmaterial för varmformning och därmed minska verktygsslitage
2012 – 2013
2012 – 2015
2013 – 2016
Målet med projektet är att sprida och öka vår kunskap om kopplingen mellan produktionsparametrar och produktegenskaper med hjälp av numerisk simulering och experimentell metodik i symbios
2011 – 2014
Syftet med projektet är att möjliggöra bättre utnyttjande av varierande digitala utvecklingsverktyg via snabb och behovsanpassad tillgång till samordnad information.
2009 – 2012
2016 – 2019
2009 – 2012
Det övergripande målet med projektet varit att skapa en stabil, tillförlitlig och verifierad process för att rengöra och ytaktivera med atmosfärsplasma inför limning av glas med/utan ceramic frit och genom det ersätta primerbeläggningen hos glasleverantör. Projektet har resulterat i en vidareutvecklad plasmaprocess, en vidareutvecklad metod för kemisk analys av glasytor samt utvärderade metoder för industriell smutsavsyning.
2013 – 2016
Projektet ska möjliggöra ett nytt sätt att arbeta med kvalitetssäkring av svetsade produkter.
2018 – 2020
Förstudien hade som syfte att sammanställa basinformation för det fortsatta arbetet i det planerade huvudprojektet och tillse att det får rätt inriktning
2012 – 2013
GAIS 2 syftar till att förbättra informations- och kunskapsutbyte inom ett globalt produktionsnätverk. Detta kommer att ske i två områden med avseende på monteringsanvisningar; Beredningsprocessen och upplärning och inlärning för montörer.
2016 – 2018
2014 – 2017
Projektet LISA2 levererar industrifärdiga tjänster som möjliggör svenskt företag att förstå och ställa sina fabriker.
2015 – 2018
Med induktionssintring ska man korta tillverkningstiden för sinterståls komponenter. Efterföljande ythärdning (med induktion) kommer att öka komponentensprestanda därmed användningsområdet för sinterståls komponenter.
2012 – 2013
Projektet förväntas resultera i att stärka svensk fordonsindustris och deras underleverantörers konkurrenskraft och samtidigt reducera miljöpåverkan från tunga fordon.
2015 – 2016
Målet med detta projekt är att säkerställa uthållig, konkurrenskraftig och robust tillverkning av högpresterande kugghjul i Sverige genom att behandla alla aspekter från optimering av driftegenskaper, verktygs- och komponentmaterial och ytbehandlingar till beredning och bearbetning av komponenter
2009 – 2012
Hypotesen är att framtidens tillverkning av lättviktsfordon drastiskt kommer att förändra fordonsmonteringen. Målet är att identifiera framtidens tillverkningsupplägg samt fortsatta forskningsområden.
2012 – 2013
2017 – 2020
3 D lightcomp.sandwichteknologin som bygger pa polymersfarer belagda med polyester resin ar speciellt anvandbar for komplexa strukturer. Den kan anvandas for stora stukturer T.ex Busskarosser, fordonschassin och batar samt for sma stukturer t.ex. extremitetsproteser och andra medical devices.
2012 – 2013
Vår hypotes är att avancerade, lätta, multilager-strukturerade kompositer med goda barriäregenskaper och skräddarsydd bionedbrytbarhet kan produceras genom att kombinera biobaserad termoplast med speciella tillsatser och massafiber-mattor. Detta material är fritt från fossil råvara, långsiktigt hållbart, brand-och slagtåligt och lämpligt för interiöra komponenter i fordon.
2012 – 2013
Projektets mål är att undersöka de synergier och möjligheter som ges av att samtidigt optimera produkten, produktionssystemet och tillverkningsprocessen i ett holistiskt optimeringsramverk
2012 – 2013
2013 – 2014
2010 – 2014
Målet är att sänka vikten på fordonskomponenter genom att använda laminatplåt med en kärna som gör att vikten sänks jämfört med att använda en konventionell solid plåt. Projektet har varit specifikt inriktat på att använda en kärna av sintrat metallpulver samt forma plåten med hjälp av presshärdningsprocessen. Provdetaljer har genomgått alla tillverkningssteg enligt plan följt av ett deformationstest. Metodik har tagits fram för att kunna simulera laminat i det genomförda deformationstestet.
2013 – 2016
2013 – 2015
Projektresultaten användes och vidareutvecklas på flera produktionsanläggningar inom VCE samt utgör underlag för såväl grund- som högre utbildning inom KTH, CTH och HV
2012 – 2014
Syftet var resultatsspridning och detta uppfylldes verkligen med 104 högkvalitativa presentationer för industri
2011 – 2012
Målet på sikt är att Sverige ska etablera en framskjuten position inom rationell och effektiv produktion av kompositer.
2017 – 2018
2014 – 2016
Hybridfogning av ultrahöghållfasta stål till aluminium med Friction Stir Welding
2012 – 2013
Målet med projektet Reducing maintenance-related waste är att utveckla och testa en generisk metod som ska underlätta för svenska tillverkningsföretag att identifiera, klassificera, kvantifiera samt reducera underhållsrelaterat slöseri inom produktionsprocesser. Målet med metoden är att tillverkningsföretagen skall kunna optimera underhållsaktiviteter och underhållskostnader utifrån extern- och intern underhållseffektivitet med hänsyn tagen till indirekt och direkt underhållskostnad.
2013 – 2016
2013 – 2016
Målet är att utveckla en CAE-baserad guide för prediktion av skärbarhet hos nya inkommande arbetsmaterial i bearbetningsprocessen.
2017 – 2020
2013 – 2015
2014 – 2017
Att öka möjligheten att använda nitrerprocesser för att skapa ytor med hög hållfasthet och friktions- och slitageegenskaper anpassade för aktuella komponenter.
2014 – 2017
Detta projekt är en fortsättning på det pågående MERA-projekt ´Metoder för modellering ochsimulering av komplett process för samtidig formning och härdning av borlegerade stål. Projektet är ett doktorandprojekt på Luleå tekniska universitet och utförs inära samarbete med Gestamp HardTech.
2008 – 2012
Projektets inriktning är att använda moderna virtuella verktyg för att modellera processen och därigenom förstå hur de dynamiska parametrarna påverkar kvalitetsutfallet.
2010 – 2011
SmoothIT-projektet kommer att utveckla modeller, metoder, verktyg och optimeringsalgoritmer för att hjälpa den svenska industrin att skapa mjukare robotrörelser, vilket minskar energianvändningen och ökar livslängden. Dessutom kommer utvecklings- och underhållsarbetet att förbättras med hjälp av verktyg för övervakning och driftsprognos för underhållsplanering.
2017 – 2020
Projektets syfte är att utveckla en processteknik för svartoxidering av borstål.
2009 – 2011
Projektet har utgått från utmaningar när det gäller gjutning och realisering av nya gjutjärn med hög hållfasthet och god skärbarhet, vägval avseende bearbetningsstragier samt materialbeteende i skärprocesser när det gäller arbetsmaterialens skärbarhet. Kisellegerat kompaktgrafitjärn har demonstreras som nytt alternativ för framtida motorkomponenter. Ny simuleringsmetodik för att hantera bearbetningsstrategier har introducerats. Generisk kunskap har stärkts när det gäller arbetsmaterialens bearbetbarhet och särskilt när det gäller sammansatta material.
2012 – 2015
2009 – 2013
Syftet är att skapa kunskap om värdeökning och kostnadsbesparing genom miljöbaserade strategier och åtgärder inom produktionssystem för verkstadsindustri.
2009 – 2012
2012 – 2015
Inom bilindustrin är designen av kaross-sammansättningsstationer fortfarande i hög grad erfarenhetsbaserad. Vidare visade MERA projektet på kopplingar mellan geometrisk kvalitet och resursutnyttjande. Därför behandlas i detta projektet konstruktionsparametrarna hos en karossmonteringsstation tillsammans, med avseende på resursutnyttjande samt geometrisk kvalitet.
2009 – 2011
Projektets målsättning var att implementera ett nytt kvalitets-system för svetsar i konstruktion och produktion av svetsade komponenter
2010 – 2012
2014 – 2015
Syftet med projektet var att öka konkurrenskraften för svensk fordonsindustri genom att ta fram enhetliga och lättanvända hjälpmedel för design och montering av optimerade skruvförband
2012 – 2014
Genom att förstå de underliggande fysikaliska fenomen i tillverkningsprocessen utvecklade och validerade detta projekt simuleringsalgoritmer.
2009 – 2012
Syftet med projektet är att forska och utveckla en effektiv prototyp på en simulerings- och visualisering mjukvara för att verifiera människa-robot samarbete. När projektet är slut finns en prototyp på en mjukvara tillgänglig, vilken har nyttjats i ett antal verifierings scenarion definierade av deltagande industripartner.
2016 – 2019
Att utveckla metoder och modeller för prediktering av verktygstillståndet i presshärdningsprocessen
2014 – 2017
Syftet med projektet var att öka produktivitet och robusthet inom tillverkande industri genom utökad användning av faktabaserade simuleringar och optimeringar. Detta har uppnåtts genom att integrera verktyg för hantering och analys av indata (GDM Tool) med simulering och optimering av produktionsflöden (FACTS Analyzer). Tidsåtgången från fråga till faktabaserat svar vid utveckling av produktionsflöden har reducerats till bara några minuter i miljöer där det finns fungerande produktionsnära IT-system.
2013 – 2017
Huvudresultatet av detta projekt kommer att vara en effektiv process för in-line geometri verifiering
2011 – 2013
Projektet ska ta fram nya arbetssätt och verktyg som möjliggör digitaliserad beredning av viktiga fogningsprocesser
2016 – 2018
Syfte och mål är att skapa industriella riktlinjer och rekommendationer gällande formning av kompositmaterial i traditionella produktionsprocesser.
2015 – 2018
Syfte: att reducera behovet av efteroperationer, minska processtider för värmebehandling och minska kassationer. Mål: ökad förståelsen för hur studerade faktorer inverkar på formförändringar vid värmebehandling
2015 – 2018
2014 – 2015
OptiDies skall skapa en djup förståelse gällande det kompletta tribologiska systemet, vilket involverar ett antal olika kompetenser; tribologi system, plåt och verktygsmaterial, nya tillverkningsmetoder för verktyg, numeriska analyser samt kostnads modellering.
2009 – 2012
Målet med projektet var snabbare produktframtagningar av hybrider och helt eldrivna lättviktsfordon. Framför allt har målet varit att utveckla metoder och digitala verktyg för effektiv geometrisk packning, monterings banplanering och analys av flexibla komponenter som rör drivlinor (framdrivningssystem) och lättviktslösningar.
2009 – 2013
2014 – 2014
Fordonsindustrin står inför en stor utmaning vid övergången till miljösäkrade fordon och produktionmed bibehållen konkurrenskraft. Nödvändiga ändringar måste genomföras snabbt, vara kvalitetssäkrade och inte påverka ledtider, en utmaning som möts av FFI Hållbar produktionsteknik och av detta projekt.
2009 – 2013
2011 – 2014
2012 – 2013
Projektets mål är att utveckla teknik för online-detektion av svetsdefekter inom fordonsindustrin med hjälp av laserinducerat ultraljud. Metoder för laser- och punktsvetsar kommer att utvecklas.
2012 – 2013
Vidareutveckling av lösningar för kraftfulla kollaborativa robotar med fokus på säkerhetsfrågor och användning av en ”enabling device”
2015 – 2018
2014 – 2018
2013 – 2016
Syftet var att ge en mer robust och bättre prediktering av verkningsgrad och livslängd av kuggkontakter i växellådor
2016 – 2018
Projektet syftar till att utveckla en ny typ av abhesion flerskiktsystem baserad på kombinationen av skikt med olika mekaniska/fysikaliska egenskaper som kan ge anpassade funktioner för slitage, friktion, vidhäftning och vätbarhet
2012 – 2013
Alla produktionsprocesser påverkas av variation vilken kan äventyra uppfyllandet av sammansättningskrav, funktionskrav eller estetiska krav. En ytterligare aspekt är svårigheten att nå önskade former i alla områden.
2009 – 2013
Syftet med detta projekt är att anpassa och demonstrera ett system för automatisk allkontroll av tillverkade komponenter.
2017 – 2020
2010 – 2011
I detta projekt tre områden för komponentframtagning inkluderas: gjutning, värmebehandling och bearbetning. övergripande mål är att åstadkomma en robust, kostnads- och energieffektiv tillverkning av komponenter för framtidens drivlina.
2009 – 2012
Främsta syftet har varit att utveckla/optimera en tunnfilmsprocess med ett korrosionsskydd lika bra som ZnPh genom studier som korrelerar processparametrar till filmstruktur/komposition och korrosion samt långsiktig prestanda.
2013 – 2017
Målet i projektet är att utveckla en industriell process för mekanisk stansnitning i multimaterial baserad på pluggfogningsmetoden.
2016 – 2019
2009 – 2012
Projektet syftar till att utveckla och hypotesprova en helt ny princip för dynamisk planering och beredning av montering, där balanseringen optimeras på en högre systemnivå, t ex ett monteringsavsnitt, snarare än på stationsnivå vilket är det vedertagna angreppssättet idag. Målet med projektet är att öka kunskapen kopplat till balansering samt vilka effekter ett produktionssystem baserat på dynamisk balansering för med sig och hur dessa relaterar till minskade systemförluster, men även vilka krav som ställs på och av människan i systemet.
2012 – 2013
Utveckla innovativa koncept för in-line OFP av värmebehandlade (härdade) komponenter, därav minimera behovet av kostsamma och tidskrävande förstörande provning.
2015 – 2018
Målet har uppfyllts genom utveckling av ny vikteffektiv skruvförbandsteknik av skruvar med hållfashetsnivå 1400 MPa
2011 – 2013
Robust lasersvetsning av aluminium med hjälp av innovativa lasersvetsverktyg och predikteringsmodeller för att undvika sprickbildning och deformationer
2017 – 2020
I projektet har vi bekräftat att modifierad anlöpning kan tillämpas för motverka/eliminera relaxation/krypning och att det kan preliminärt kopplas till stabiliteten hos mikrostrukturen hos det anlöpta sinterstålet. Ny metodik för utvärdera sintermaterials potentiella relaxation/kryp har etablerats och ny kunskap har etablerats. Ett potentiellt nästa steg är att se hur andra sinterstål kan optimeras och hur en modell för prediktering av kryp/relaxation hos sinterstål vid måttligt förhöjd temperatur kan utvecklas.
2012 – 2013
Utveckla tillverkningsteknologier där komposit integreras direkt mot metall i produktionssystem för presshärdning av borstål och varmformning av aluminium.
2015 – 2016
Förstudien omfattar en litteraturstudie, test av olika elektrokemiska tekniker och utformningen av en förenklad uppsättning för att utföra LECD. I slutet av projektet bör det vara möjligt att bedöma om LECD kan utvecklas till en metod för lokaliserad elektrokemisk deponering i samband med återtillverkning.
2015 – 2016