Magnus Wiktorsson
Professor in Production logistics
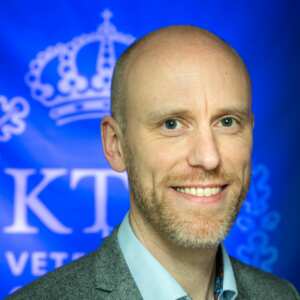
Project time: 2023 – 2026
Budget: 19 000 000 sek
Dynamic SALSA - Dynamic Scheduling of Assembly and Logistics Systems using AI
The EUREKA SMART project Dynamic SALSA will develop Ai solutions and practical software applications for dynamic scheduling technologies in smart assembly and logistics including novel digital services based on ICT for the automotive sector. The project will achieve a unified framework and interoperable platform, and practical shop floor applications for end-to-end engineering in smart manufacturing including Ai, digital twins, Industrial Internet of Things, and vision-based system for data gathering. The project consortium includes original equipment manufacturers of the automotive sector, SMEs specialized on ICTs, and universities from Sweden and South Korea with expertise in the use of Ai and digital twins in smart assembly and logistics. The major results of this project include the development of theory, algorithms, and demonstrators from universities; functions, modules, and packages from SMEs in ICT; and floor shop applications and demonstrators for LEs. The project identifies key performance indicators of economic, environmental and social sustainability for measuring its achievements.
Knowledge is needed that can support design and control of automation in material handling systems.
2019 – 2022
The objective is to bring together expertise from AI and LCE to Product/Service Systems for Swedish manufacturing firms in a multidisciplinary research effort to utilise latest techniques efficiently for Swedish production industry. The goal is to make a plan of developing demonstrators in production and maintenance using artificial intelligence techniques, digital technologies and lifecycle engineering methods
2019 – 2019
Hybrid joints, combination of gluing and mechanical joining are highly demanded where several materials are to be used and assembled. HJT therefore focuses on the smart factory's ability to create flexible production with simulation and programming in a digital twin that combines the latest technology for bonding, assembly and mechanical joining, rheology based simulation and automated collision-free planning. The projects goal is to focus on the whole hybrid joining process and to establish a testbed for hybrid joining as a resource for Swedish Industry.
2017 – 2020
The project aims to use deviation data for improving the product design and production.
2020 – 2023
Demonstrate solutions for visibility in production logistics, for dynamic abilities and resource efficiency.
2019 – 2022
This project intends to design and develop a new test methodology for evaluation of power flowability in powder bed fusion (PBF) systems. The test apparatus will simulate powder flow in PBF machines and can be used for optimizing the powder layering behavior for potential utilization of alternative powder qualities. Additionally, this equipment creates opportunities for both powder producers and AM part manufacturers to minimize powder waste and maximize material utilization.
2017 – 2018
To create an inventory of AI techniques for maintenance services, apply AI techniques to three industrial cases, and evaluate their economic and environmental implications.
2017 – 2019
Develop and validate predictive maintenance algorithms based on AI and ML. The vision is failure free production
2019 – 2022