Mikael Malmström
PhD, Senior researcher
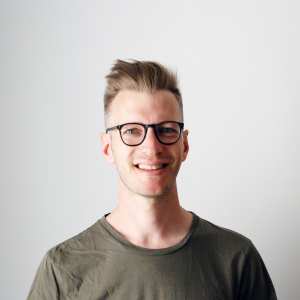
Project time: 2021 – 2024
Budget: 9 842 800 SEK
Funding: SIP Produktion2030
Measure hardening depth and hardness with laser ultrasonics for resource efficient hardening processes
At present the automotive industry hardens critical parts in crankshafts by induction hardening, e.g., for heavy trucks, dumpers, excavators etc. The process parameters for the induction hardening are usually verified by time consuming destructive testing before- and after a production-campaign (days-weeks). In a worst-case scenario, the destructive testing after the campaign detects that the quality of the hardened surfaces is below acceptable levels which might require that the whole batch must be scrapped. The problem with verifying the quality of hardened surfaces will also be present in the future when mobility is primarily electrified and the only solution is an integrated system based on a non-destructive testing (NDT) method. In a previous project (OFP4p) laser ultrasonic (LUS), which is a non-destructive testing method (NDT), played a relatively small part but nevertheless showed great potential. The major advantage with LUS, compared with other NDTmethods, is that it is a contact free method and is therefore more suitable for inline automation and implementation in complex industrial processes. The REAL project goal is to enable true in-line non-destructive verification of hardness/hardening depth by using laser ultrasonics and thus increase the resource efficiency by minimizing scrapping an in some cases removing the waiting time associated with the old-fashioned destructive testing.
Vinnova dnr: 2021-03683