Johan Berglund
Ph.D. Manufacturing Technology
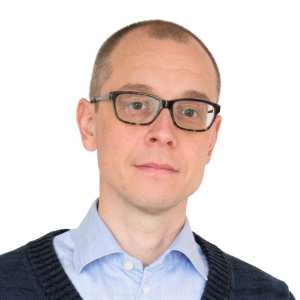
Project time: 2016 – 2018
Budget: 9 750 000 kronor
Funding: SIP Produktion2030
Reduced lead times and improved performance for tooling through innovative manufacturing and assembly strategies as well as optimised design enabled by use of additive manufacturing (AM).
AMtoFlex will strengthen the competitiveness of the Swedish manufacturing industry through improved production flexibility in the tooling manufacturing industries by novel design, manufacturing strategy, and assembly strategy through usage of emerging and novel technology like Additive Manufacturing (AM). In the tooling industry, the main challenge having a negative impact on the Swedish manufacturing industry is lead time, that on average is about 11 weeks, and for large and complex tools, as used in the automotive industry, can be as long as a year. Through utilization of AM, it is possible to address near-net-shape manufacturing incorporating internal cooling channels and removing time-consuming subsequent subtractive operations, and through digitalized approach work with a flexible supply chain. In addition, the AMtoFlex route will also be beneficial to tool performance; i.e. reducing the cycle times and improving
component quality. AMtoFlex contributes also to sustainable manufacturing through
significantly reducing the material waste, high material utilization in AMtoFlex route, beneficial for circular economy.
2014 – 2016
2017 – 2018
Assessing the Robustness of the Laser Powder Bed Fusion Process
2021 – 2024
2013 – 2016
The project aims to develop a new cyber-physical framework to realize extremely flexible production.
2021 – 2024
2017 – 2020
2017 – 2018
2013 – 2016
2016 – 2016
2016 – 2016
RemProLife aims at improving the use of life-cycle information to achieve more efficient remanufacturing from economic and ecological perpectives.
2013 – 2016
2016 – 2016
2015 – 2016
2015 – 2016
2013 – 2017
2017 – 2021
Tooling constitutes a significant part in the economical investment of the hot stamping process. Significant benefits in production economy and environmental benefits can be attained by improving the tribological performance in hot forming operations of automotive components. The main idea of this project is to create tailored tool surfaces on dies made from cheaper and easier to manufacture tool steel for the hot stamping of ultra-high strength steels.
2015 – 2018
The overall goal of DiSAM is to create a unique test AM Hub in Sweden for metal and polymer based additive manufacturing processes.
2017 – 2021
2015 – 2016
2017 – 2018
2016 – 2019
2014 – 2017
2017 – 2018
IDAG aim to identify gaps and propose actions for the digital infrastructure necessary to industrialize additive manufacturing technologies. Actors from a new type of value chain of manufacturing companies – from powder to product – collaborate with digital solution providers and researchers to understand the needs and articulate the necessary actions through analysis of industrial cases. The target is to deliver a description in the form of a roadmap for how these actions can be developed and provided in order to ensure flexible and scalable digital platforms for additive manufacturing value chains.
2019 – 2019
Robotic solutions with autonomous decision-making software supporting on-demand production using resource pools.
2021 – 2024
The project's main goal is to develop a design and manufacturing methodology, for resource efficient additive manufacturing of components in the automotive industry.
2017 – 2020
2016 – 2018
2015 – 2016
2015 – 2016
2015 – 2015
2015 – 2016
2014 – 2017
2014 – 2017
2016 – 2017
2016 – 2016
This project intends to design and develop a new test methodology for evaluation of power flowability in powder bed fusion (PBF) systems. The test apparatus will simulate powder flow in PBF machines and can be used for optimizing the powder layering behavior for potential utilization of alternative powder qualities. Additionally, this equipment creates opportunities for both powder producers and AM part manufacturers to minimize powder waste and maximize material utilization.
2017 – 2018
2014 – 2017
2015 – 2015
The project focuses on economic and environmental sustainability and increased industrial competitiveness.
2017 – 2018
With globalization and other megatrends as demographic changes and climate change, more knowledge is needed regarding production in an international perspective. PADOK Study Visit in India 2016 have given an increased knowledge regarding how production is conducted in India, some of the challenges producing companies in that region is facing and how Swedish companies interested in investing in production in India could act to establish themselves in the region.
2016 – 2016
2015 – 2018
2013 – 2017
The SAPPA project is about innovative cloud-based predictive and preventive maintenance systems, improving availability of products and production systems.
2014 – 2016
2015 – 2016
2014 – 2017
2015 – 2016
The goal is to demonstrate the additive manufacturing of micrometer/millimeter wave components.
2019 – 2022
Design process from concept to printable stl-file for AM including surface based networks in the structure.
2019 – 2022
2017 – 2020
2014 – 2018
Every manufacturing company measure and control production performance with a system of KPIs. The aim of the SMART-PM project is to investigate and demonstrate new ways of collecting data, transforming data to information and introducing new decision tools based on valid information and economic models of the production systems.
2018 – 2020
2017 – 2019
DiLAM strengthens the competitiveness of the Swedish manufacturing industry by aligning the digital and physical supply chains for additive manufacturing of large parts.
2017 – 2020
The aim of the project is to demonstrate utilization of additive manufacturing for copper-based products and process solutions and faster adaption
2016 – 2018
2017 – 2018
DIDAM develops and demonstrates digitalization solutions to industrialize Additive Manufacturing
2020 – 2023
2017 – 2018
2016 – 2017
Increased sustainability and cost effectiveness through improved strategic decision-making in production issues based on new metrics system for production and development.
2015 – 2017
2014 – 2017
2014 – 2014
2017 – 2018
This project aims to contribute to the development of future ERP-systems. The project will explore how to offer work, redefine work roles and challenge companies to make use of advanced systems support and the technology within and around these. Overall, the project aims to contribute to the development of both the next generation of ERP-systems and a complementary change in the way firms see upon work organization, so that technology can support and meet the needs of the humans within organisations rather than enforcing structures upon them.
2019 – 2019
The project aims to test the idea of an effective circulation system for material waste from additive manufacturing. Our goal is to map the prerequisites for closer collaboration between material suppliers and additive manufacturers, including new business models, partnerships and logistics solutions.
2017 – 2018
2015 – 2016
2017 – 2018
2015 – 2017
2015 – 2016
2015 – 2016
2016 – 2018
2017 – 2018
The main idea of the project is to investigate and demonstrate how the digitalized and proven systems and technologies of the Process Industry, like CPAS, can be used in DM to improve competitiveness and drive growth
2017 – 2019