Jan-Eric Ståhl
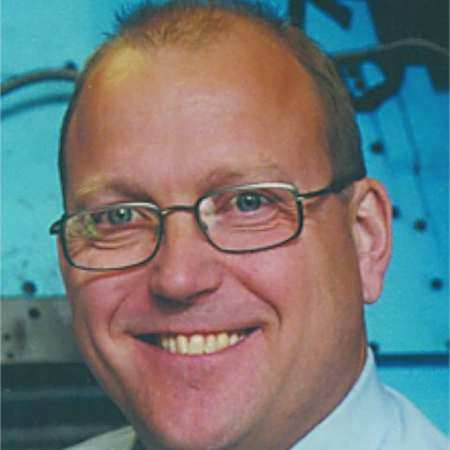
Project time: 2020 – 2022
Budget: 11 000 000 kr
Reduced variation in machinability promote lower costs, predictable and a sustainable processing of grey cast iron components.
The project aims to reduce the impact and variation of grey iron machining performance and aims to achieve a predictable and sustainable manufacturing process. The work is based largely on the results of ongoing projects that now are under completion. Through this project, the project team expects to further develop, adapt and complement current experiences and know ledge that enable a full-scale implementation of project results. This w ill provide a predictable and sustainable production of grey iron components and associated quality control and methods for performance analysis. Lower costs associated with downtime, scrap and speed losses in combination with lower tool costs shall mean achieved through optimized metal cutting data and optimized tool selection as w ell as the changing requirements for cold aging and trace elements regarding level and distribution in the castings. The results will also provide the basis for specifications on cast blanks, machine and tool purchases. Know ledge of the so-called spin-off character can also be adapted for other types of cast irons and to some extent other metal alloys.
Vinnova dnr: 2019-03118
Today, the industry often uses energy- and time-consuming autoclave processes for the manufacture of composites with high quality requirements, towards for example the aerospace industry.
2017 – 2018
Implementation of thin film pre-treatments to replace ZnPh for a more sustainable and cost-efficient production.
2019 – 2022
Urinary incontinence is a common problem that affects everyone, ranging from young women who have recently given birth to men who have undergone prostate surgery. Amongst people over the age of 70, almost half of everyone, both women and men, suffer from involuntary urine leakage.
2021 – 2023
Indium is a silvery metal that is very soft and malleable. Together with tin, the metal can be used to create indium tin oxide with properties that make it one of the most important components in the electronics industry. The goal of the project is therefore to build a recycling unit in a continuous production without waste.
2021 – 2023
Cyclicor, which has its origins at Lund University, has in a previous project within Mistra Innovation successfully developed a method for producing the plastics polycarbonate (PC) and polyurethane (PU) without toxic additives. One goal of the Polyfree 2.0 project is to increase the production of the new plastics from lab scale to quantities that enable the participating industrial companies in turn to take steps towards finished products. Other goals are for the plastics to be recyclable as well as have the required properties.
2021 – 2023
The project will investigate a new method to reduce raw material waste in the manufacturing industry.
2022 – 2023
The project aims to test the idea of an effective circulation system for material waste from additive manufacturing. Our goal is to map the prerequisites for closer collaboration between material suppliers and additive manufacturers, including new business models, partnerships and logistics solutions.
2017 – 2018
To lay the foundation for tomorrow’s network of circular economy microfactories producing products designed by Swedish industry and produced from local recycled plastics.
2022 – 2023
For more than a hundred years, lubricants for various types of machines have mainly been made from fossil oil. The function has improved over time, but they also have disadvantages; they negatively affect the environment, human health and the climate. The project will therefore work to improve the practical applications by, together with other tests, combining lab tests with field tests.
2021 – 2023
The project's goal is the circular use of plastic in cars through reuse and recycling.
2023 – 2025
Urinary incontinence is a common problem that affects everyone from young women who have recently given birth to men who have undergone prostate surgery. Amongst people over the age of 70, almost half of everyone, both women and men, suffer from involuntary urinary leakage.
2021 – 2023
A large number of building boards are used in both construction and furniture manufacturing. They are usually made of sawdust with a formaldehyde-based adhesive as a binder. However, they have some problems, including the fact that shavings absorb moisture and that formaldehyde is both allergenic and potentially carcinogenic. The LigniGC project aims to develop a better alternative.
2021 – 2023
The REWIND project combines the principles of lean production and eco-efficiency in three industry pilots at Stena Recycling, Volvo AB and IKEA GreenTech. The objective is to retain the value embedded in materials with circular strategies (reuse, remanufacture, recycle, repurpose, etc.). Lessons learnt from the pilots will be used to develop educational tools for engineers and industry leaders to accelerate the uptake of best practices for circularity and sustainable production.
2019 – 2022
A research collaboration between Luleå University of Technology and the company RGS 90 will provide new treatment methods for three common but problematic types of waste.
2015 – 2019
Reduce the environmental impact of foundries by reducing the amount of sand waste using machine learning.
2023 – 2024
The project aims to improve the collection system for recycling of pre-consumer plastic waste.
2022 – 2023